触れずに検査!?「非破壊検査」で挑む業界ゲームチェンジャーへの道
2025/04/11 Toshiba Clip編集部
この記事の要点は...
- 原子力の技術から生まれた!金属を熱いうちに検査する、溶接同時検査を実現するレーザ超音波検査技術とは?
- 検査位置把握をデジタル化!カメラをつけるだけで検査の負担低減を実現した革新的技術とは?
- 新規事業開発部門とタッグを組み、顧客から徹底的にヒアリング!
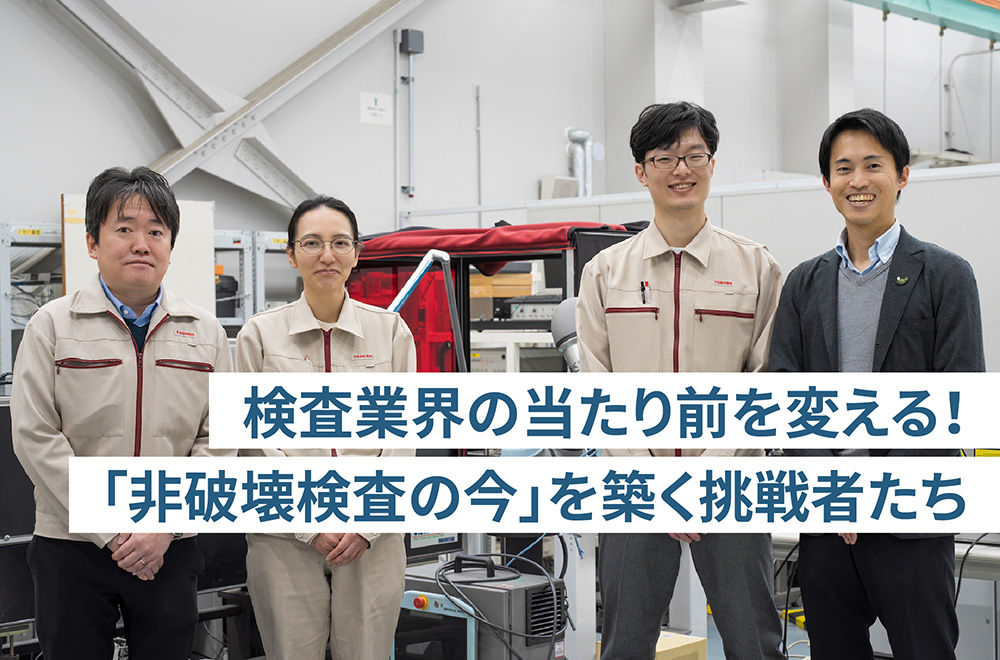
数年前、エジプトの大ピラミッドに、これまで知られていなかった大きな空間が発見された。これは、ミューオンという素粒子の物質を透過する性質を利用した調査によるものだ。もちろん、歴史的価値のあるピラミッドに傷を付けることなく調査が行われた。このように、対象物を破壊せずに内部の状態を探る方法は、非破壊検査と呼ばれ、身近な物では、レントゲン検査による人体の内部の可視化診察などもその一種である。切断したり、破壊したりせずに内部の状態を知ることのできる非破壊検査は、あらゆる分野で利用されている。
東芝でも、医療・産業を問わず、様々な分野の非破壊検査技術をリードしてきた。今回は、東芝が手掛けるUT(Ultrasonic Testing)と呼ばれる超音波を用いた非破壊検査に関する革新的な技術をご紹介。レーザ超音波を用いて検査するレーザUT技術、デジタルで検査位置を簡単に把握するUT位置自動計測システムの2つの最新非破壊検査技術について、開発担当者が語る。
「その検査、触らずにできます」溶接しながらの検査を実現するレーザUT技術とは
自動車や鉄道、橋や建物など、私たちの身の回りにあるモノは、溶接によってできている場合が多い。金属などの二つ以上の材料を熱や圧力を加えて接合する溶接は、産業分野では欠かせない技術の一つである。しかし、接合される溶接部の強度や品質を高く保つためには、高度な技術が必要とされる。また、外観から内部の品質状態を知ることが難しいため、溶接後には非破壊検査による品質確認が求められる。
通常、溶接部を超音波で検査するためには、検査する部分にジェル状の接触媒質を塗ってセンサを接触させる必要がある。そのため、高温となる溶接部が十分に冷えた状態になるまで検査はできない。
「溶接部にレーザ光を照射して超音波を発生させることで、溶接部が高温のままでも検査できる『レーザUT技術』を開発しました」そう語るのは、東芝エネルギーシステムズ株式会社の菅原あずさ氏だ。
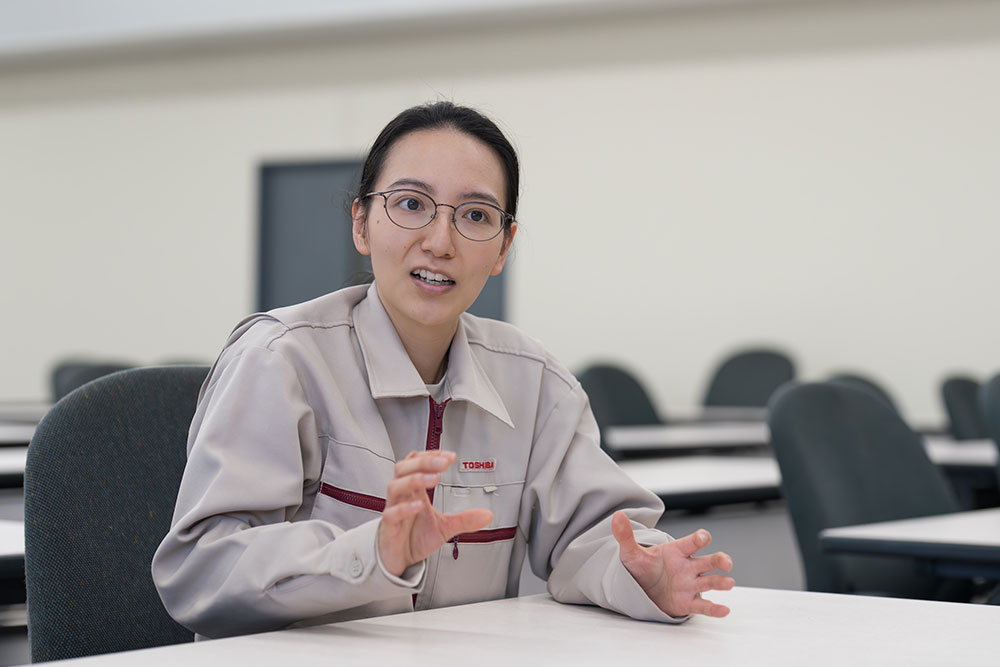
レーザUT技術は、非接触で検査できるため、高温の対象物でも検査が可能。これにより高温状態にある溶接部も、溶接しながら検査できるため、従来のように溶接工程後の検査で見つかる不良の補修・再溶接を行う必要がなくなり大幅な効率化が可能となる。現在、自動車部品や他の機器の検査を行う様々な会社が興味を持っており、2025年には本格的に溶接機を扱う他社とともに溶接機開発を実施予定だ。
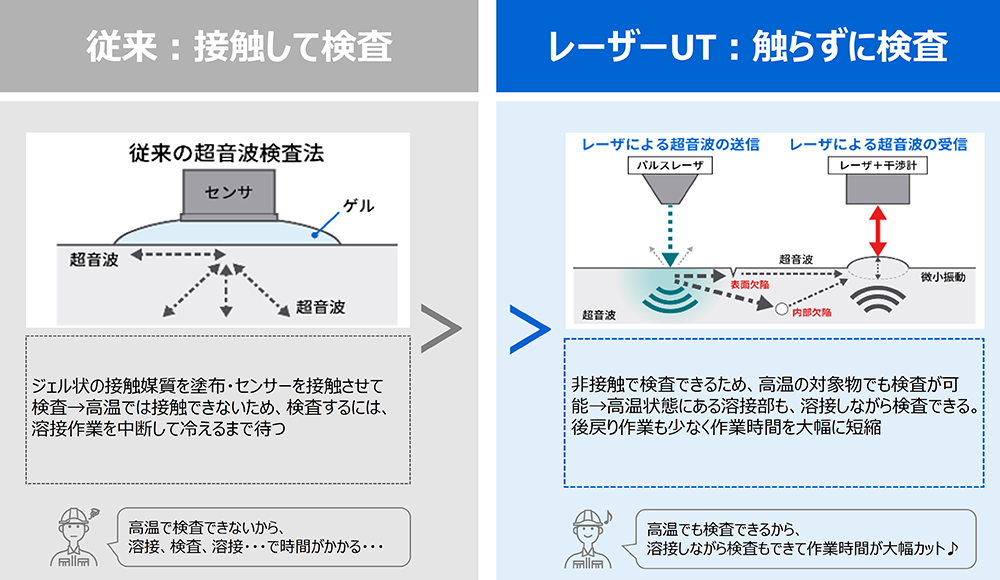
レーザUTのメリットはこれだけではない。従来の超音波検査ではセンサが届かなかった狭い場所への検査にも道を開くという。
「光ファイバによってレーザを伝送することで、溶接機に搭載することができるようなサイズに、検査ユニットを小型化することができました」と、東芝エネルギーシステムズ株式会社の星岳志氏だ。

前述のとおり、従来の超音波検査では、ジェルを塗布してセンサを当てて検査する必要があった。すなわち、触れない場所は検査できなかったのだ。
しかし、レーザUT技術により、溶接機へ検査装置搭載が可能となることで、溶接しながら、溶接できるところを全て検査することができるようになる。これは、溶接製品の品質と信頼性を大幅に向上させる技術であると言えるだろう。
このレーザUT技術、そもそもなぜ東芝が開発できたのだろうか。その原点は、原子力発電所向けの検査技術の開発にある。
「2005年1月、東芝は、原子力発電所の検査に、世界的にも前例のないレーザ超音波法を採用し、原子炉内機器へのレーザUT適用に成功しました。人が立ち入ることのできない原子炉内での検査方法として考案されたのが、我々のレーザUTだったのです」(星氏)
しかし、溶接作業で用いるレーザUT技術の実現の裏には、レーザ光による超音波検査というアイデアだけでは成し得なかった、多くの苦労があったと菅原氏は語る。
「実際の溶接作業では、想定していた以上の振動と、照射位置確保の問題がありました」(菅原氏)
溶接機に取り付けたレーザUT装置が、溶接機のレールに沿って動く際に、振動によりレーザの照射位置がずれてしまうこと。さらに、溶接面が斜めに傾斜している場合、レーザをまっすぐに照射することが難しいという二つの問題が開発陣を悩ませたという。
「研究室でうまくいっても、現場で使えないと意味がないんです。そんな時は、答えは現場で見つけられると考えて何度も現場の技術者の意見を聞きに行きました」(星氏)
度重なる現場との試行錯誤の結果、レーザ照射位置のずれに対しては、ボールローラを搭載した台車のような装置を開発し、ボールローラを溶接面に沿わせながらレーザを照射することで、一定の距離と照射角度を保つようにすることで解決する。
これらの対応策を持って、実機と同じ溶接機と走行レールを使用して溶接部にレーザを当てることを繰り返し最適な照射位置を探すことで検査精度を高めていった。
「自分たちが作る技術を、実際に試すことができる環境がグループ内にあるというのも、東芝の強みなんだと再認識しました」と菅原氏は振り返る。
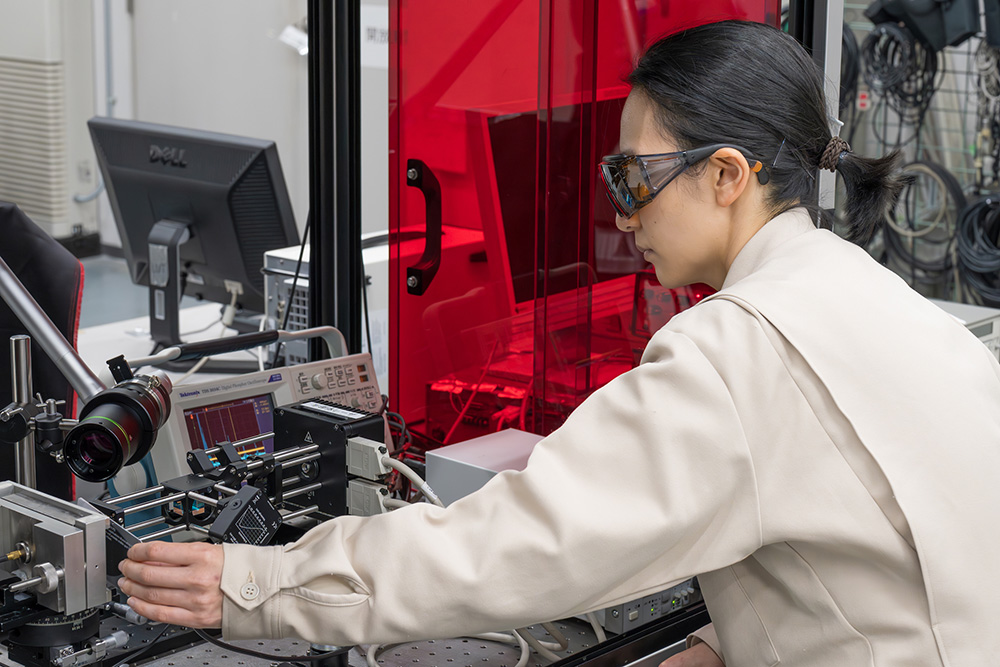
検査をデジタル化!?カメラで検査位置を簡単に把握するUT位置自動計測システム
次に紹介するのは、非破壊検査に欠かせない検査位置の特定をデジタル化した、UT位置自動計測システムだ。このシステムは、検査員が抱える作業負担を大幅に減らし、これまでの超音波検査の工程を半分程度に短縮できるのではと期待される技術である。
通常、超音波検査では、センサを当てる部分を少しずつ移動させることで、必要な範囲の検査を行い、センサの位置を特定しながらその位置の超音波検査結果を記録していく。様々な形状や検査範囲に対して自在にセンサを動かすために、手動でセンサを移動させるのが一般的だ。しかしこの場合、目的の位置に正確に移動させるための事前準備として検査対象にケガキ(対象物の上に目印となる線を描くこと)を行う必要があるだけでなく、センサの検査位置を人の手で記録していくことも必要だ。
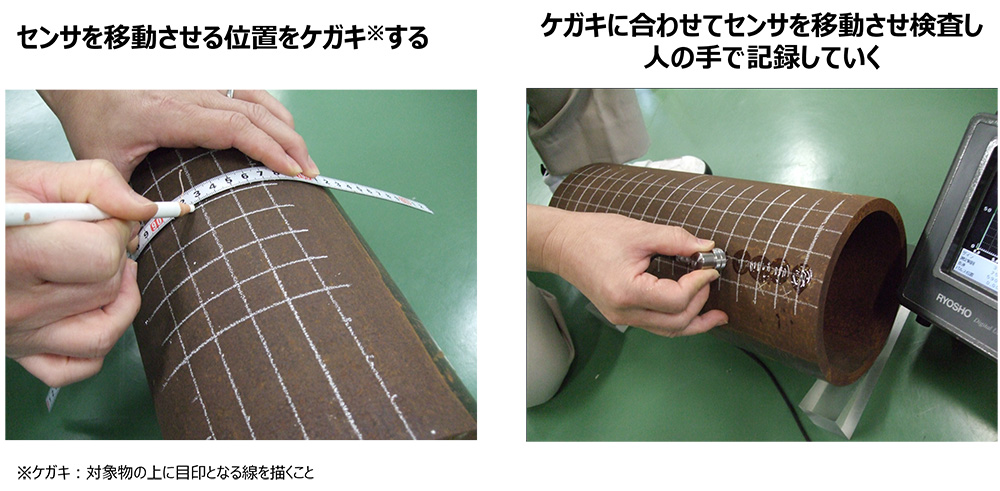
「UT位置自動計測システムが、これまでの検査と革新的に違うのは、こうした事前準備なく位置を計測し同時に記録もできるところです」そう語るのは、東芝エネルギーシステムズ株式会社の中島弘達氏である。
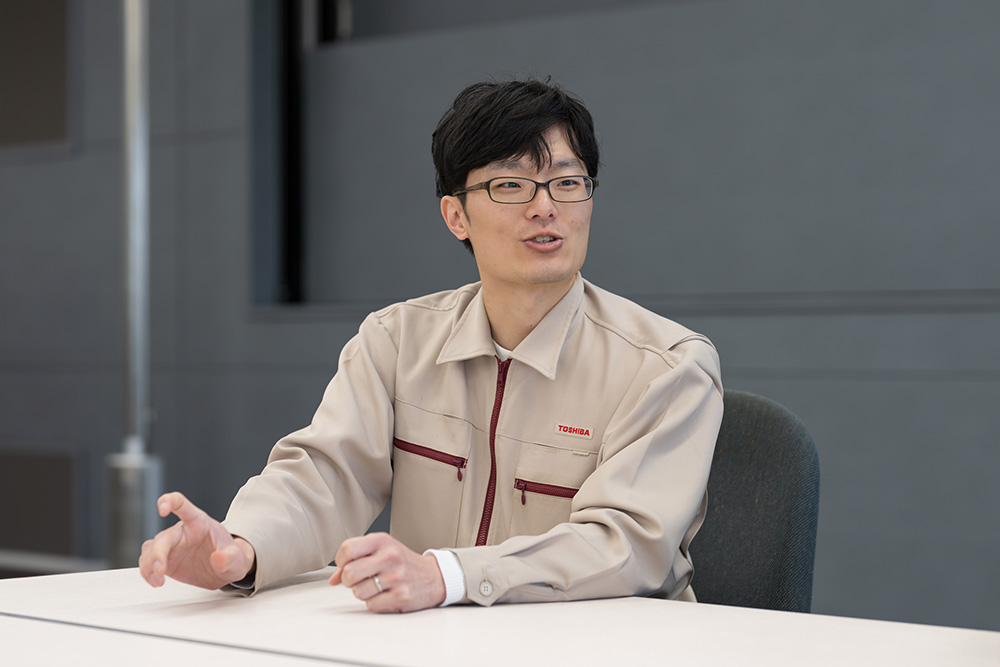
中島氏によれば、UT位置自動計測システムは、シンプルな要素で構成され、手動で移動させたセンサの位置を手軽に計測可能にする技術だという。いったいどうやってセンサの位置を計測できるのだろうか。
「UT位置自動計測システムは、カメラを使って周囲の環境を撮影することで、センサの位置を特定し、デジタル化する技術です」(中島氏)
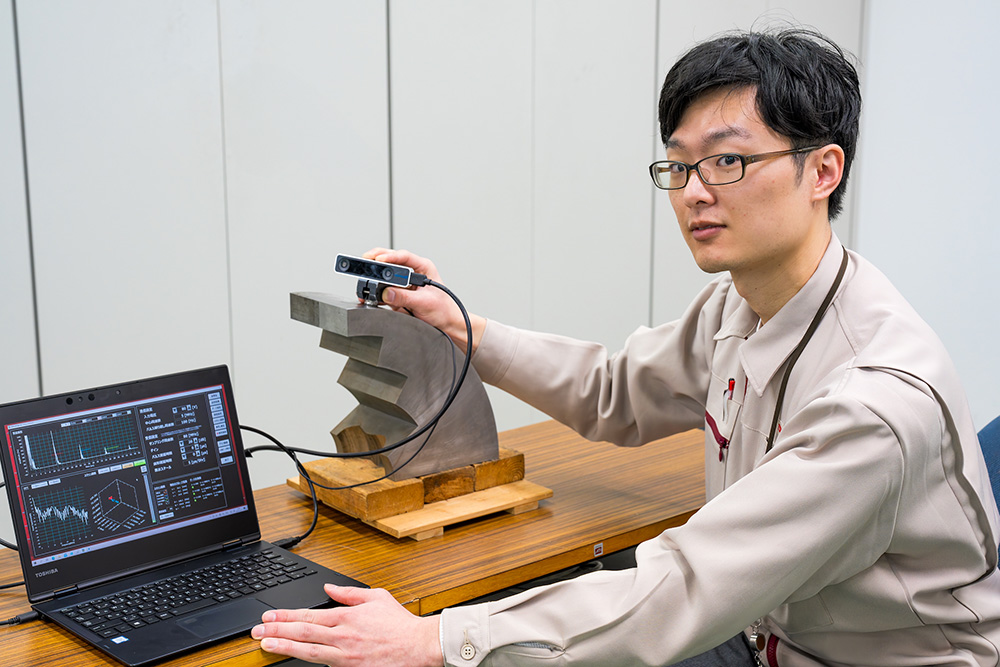
UT位置自動計測システムでは、センサではなく、周囲を撮影した画像によって相対的な自身の位置を特定する。このため、様々な形状でも、センサに取り付けられたステレオカメラが捉える周囲の画像の変化によって、センサ自身の移動を正確に特定するのだ。
ステレオカメラは、人間の目と同じ、位置の固定された二眼による視差を利用して奥行きを含めた空間の認識を正確に行う。以前は奥行き感のある3D画像を生成するカメラとして利用されていたが、近年は、自動車の運転支援システムなどで改めて注目されている技術だ。
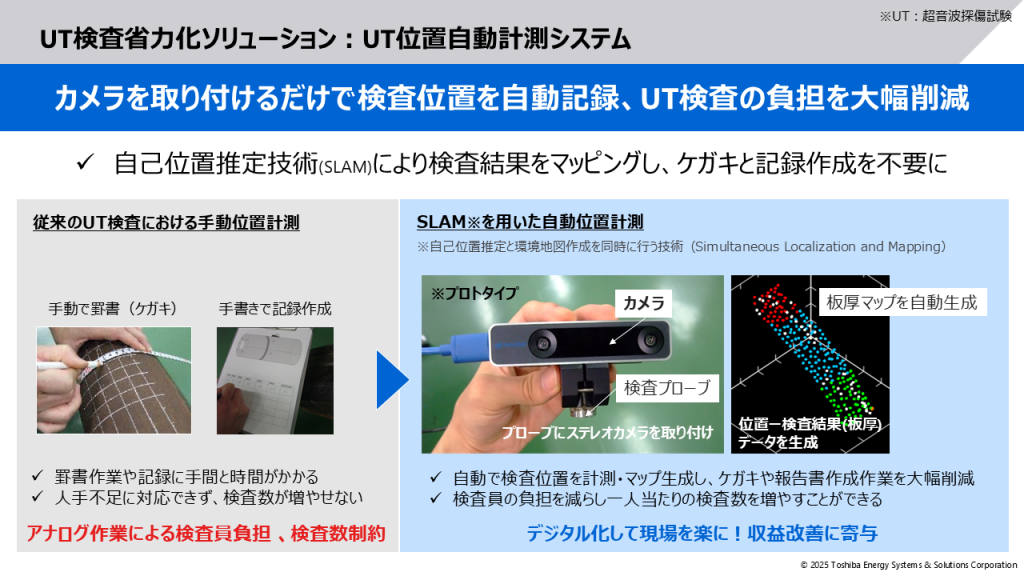
センサの位置を自動的に計測して記録する装置は、以前から存在していたという。しかし、それらは数千万円のオーダーで非常に高価な製品が多いという。これに対して、UT位置自動計測システムは検査装置にカメラを取り付けたもので、コストを1/10程度に抑えることもできるため、より多くの現場で利用されることが期待できる。
中島氏は、センサに取り付けたカメラで環境を撮影して位置を把握するというアイデアの実現には、カメラや映像解析を専門とする東芝グループ内のチームから得た、技術的なアドバイスが重要だったと語る。
「困ったことを身近な人に相談すると、その人がより答えに近いと思われる人に聞いてくれます。そうしたことを繰り返して、あっという間に専門家の意見が得られる。これが東芝グループの良いところだと実感しました」(中島氏)
技術開発の次なる壁──どう売るか?
技術開発にある程度めどがついたころ、次の課題が中島氏を悩ませた。「どう売りこんでいくか」だ。特に検査業界の場合、古くから定着している検査技術を変えるというのは、容易なことではなかった。中島氏がビジネス化に腐心していたとき、声をかけたのが新規事業開発部門だった。
「技術を開発しても、実際に活用してもらわなければ意味がありません。新規事業開発の専門家からアドバイスをもらうことに、迷いはありませんでした」(中島氏)
この検査技術のデジタル化のサポートを買って出たのが、東芝エネルギーシステムズ株式会社 新規事業開発部の武田知弥氏だ。もともと原子力の技術部門畑の武田氏は、東芝の新たな事業のタネを育てたいという熱い想いで新規事業開発部門への異動を希望した。
「まずは、検査に関わる色々な会社に一緒にヒアリングに行きました。我々の技術を知ってもらうことももちろんですが、想像ではなく、顧客の実際の困りごとを詳細に聞かなければ、真の意味でのソリューションには繋がらないと思っていたからです」(武田氏)
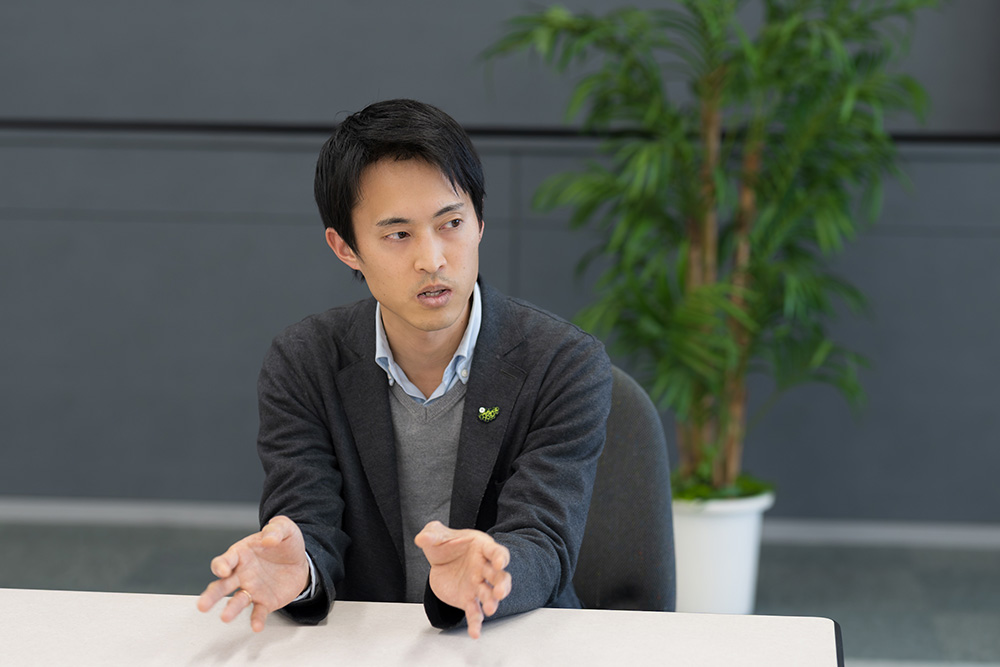
これまで顧客へ説明する機会があまりなく不安だった中島氏も、何度か経験するうちに慣れていき、仮説通りニーズがあった課題と新たな発見があった点を整理できたという。さらに、当初の想定と異なった企業から熱烈オファーがあった。
「顧客課題起点でヒアリングをしたことで、自分たちの技術は、まずはプラントのような大型構造物の検査をしている会社にニーズがあると分かりました。これも実際に会って検査手法の詳細を聞かなければわからなかったことです。足を運ぶことがどれだけ大事かを気づかされました」(中島氏)
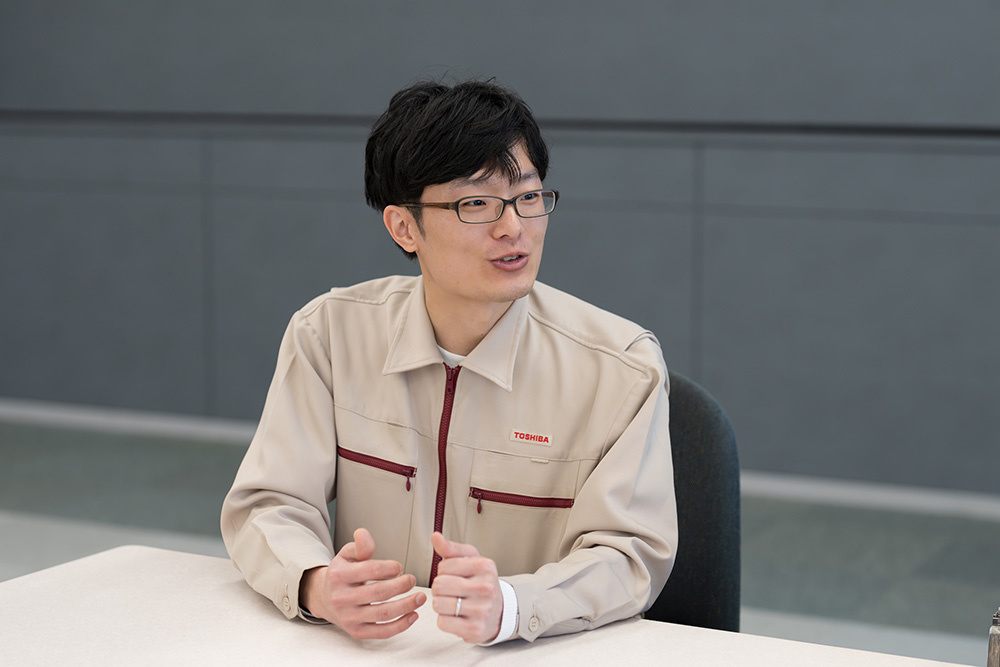
武田氏は、オファーがあった時のことを振り返る。
「確かに、時間のかかるケガキなどの事前準備や記録作業がなくなるという点は、原子力発電所や化学プラントなど、検査期間の短縮が求められる場所で大きな力を発揮すると期待されます。それと私が感じたことなのですが、技術力の高さはもちろん、中島さんのプレゼンに、すごく熱意を感じたのです。そして楽しそうにやっている。それがお客様にも伝わって、この人と一緒にやっていきたい!って感じさせたのもあると思います」
中島氏は最後に、UT位置自動計測システムが、検査技術の当たり前の選択肢の一つとなることを目指すため、検査に携わる多くの人に試してもらいたいと語った。
「今、ありがたいことに検査に携わる様々な会社から問い合わせを頂いています。話をしてみると、最初は手で検査の位置を測るのが普通だったけれど、我々の技術を紹介すると、実は今のやり方が不便だったことにお客様も気づかれるなど、これまでの当たり前を見直されるきっかけになったのではないかと思います。私たち自身も、新たな発見がたくさんありました。だからこそ、これからも実際にお客様の現場の環境や困りごとを積極的に聞きに行き、お客様と一緒に社会への実装を探っていく。最終的には、検査業界の当たり前を変えるゲームチェンジャーになっていきたいと思います。」
時間やコストがかかる非破壊検査技術だが、新たなアイデアで与えるインパクトは大きい。あらゆる領域の検査をより正確に、よりスムーズにしたいと願う熱量はやがて、新しく生み出される製品の品質向上にもつながるだろう。検査業界を変え、ひいてはどんな社会に変えてくれるのか、楽しみだ。
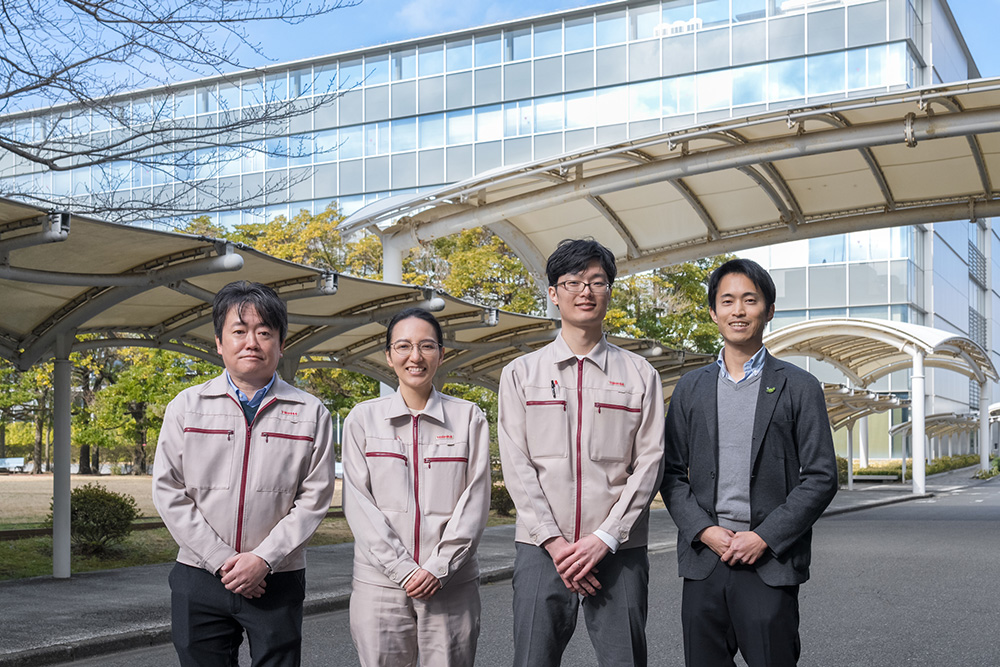
関連サイト
※ 関連サイトには、(株)東芝以外の企業・団体が運営するウェブサイトへのリンクが含まれています。
レーザ超音波法による非破壊・非接触検査 「その検査、触らずにできます!」 | 特集・トピックス | 東芝エネルギーシステムズ