環境変化に負けないモノづくり。東芝のAI技術による、人と機械の役割分担。
2020/06/17 Toshiba Clip編集部
この記事の要点は...
- モノづくりの最適化・自動化を進め、人は創造的な仕事に集中
- 人間が感覚で製品の品質を判定していた『官能検査』を、AIが担当
- 現実空間とサイバー空間をつなぎ、自律型の溶接システムを開発中
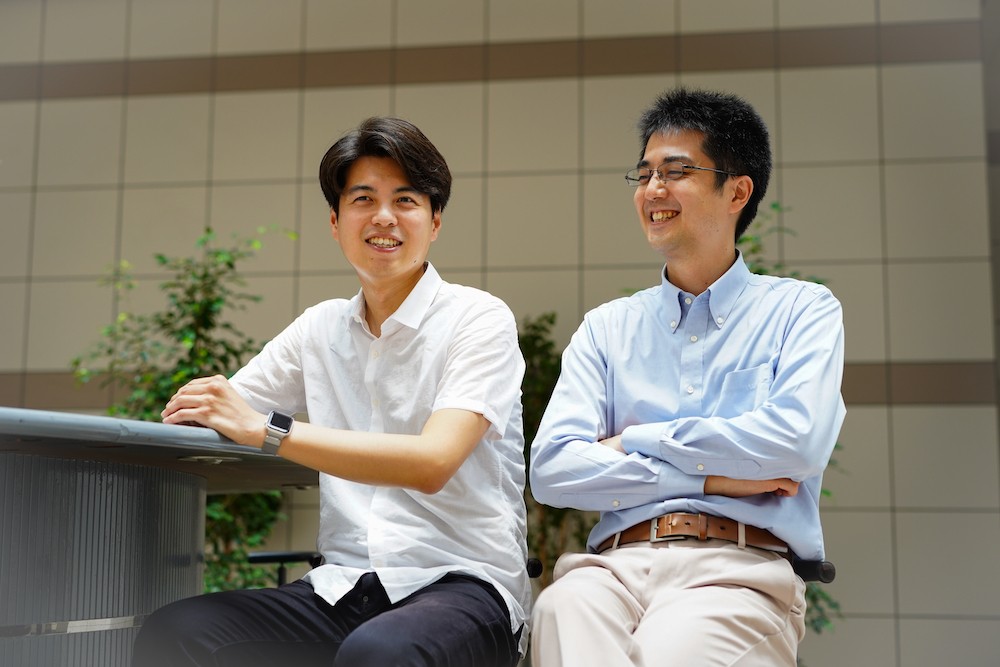
ヒトやモノのデータが即座に共有され、つながる世界。企業が競争力を確保し、新型コロナウィルス感染症等による環境変化においても、社会インフラを中心とした価値を継続して提供するためには、現実世界のデータをどう収集・解析して、再び現実世界へとフィードバックするか、その巧拙が問われる。
東芝は、データとAI技術の組み合わせによる自動化で機械に任せられるプロセスは機械に行わせ、人は人にしかできない創造性を発揮することで、環境変化に強い体制を構築し、140年以上の歴史を持つモノづくりを革新しようとしている。その最前線の動きを追った。
匠の技を、データを介してAIに実装
ヒトやモノが生み出すデータは増え続けており、企業のあり方や、競争原理を変えている。膨大なデータをどう活用し、価値へと結びつけるのか。今、企業にはイノベーションが求められている。具体的には、多様かつ大量のデータを収集し、それを人工知能(Artificial Intelligence: AI)で解析し、いかに社会課題の解決へつなげられるかが問われている。
AIについては、2016年に「AlphaGo(アルファ碁)」がプロ棋士に勝利するなど、深層学習の技術が注目されている。深層学習では、何層も積み上げられたネットワークに多くのデータを機械学習させることで、複雑な事象の解析が可能になる。では、社会の主要プレーヤーである企業は、データとAIの組み合わせでどのような価値を生んでいるのだろうか。
例えば、製造業。東芝では、モノづくりの企画・営業、開発・設計のプロセスから、据付や保守というプロセスまでをデータで一気通貫につなぎ、AIによる解析を通じて品質・納期・コストのバランス最適化などの価値を生もうとしている。製造業の競争領域は、今や完成した製品だけではなく、そのバリューチェーン全体に及んでいるのだ。モノづくりの最適化・自動化が進めば、人は創造的な仕事に集中でき、次の新たな価値を生める。
また、モノづくりの最適化・自動化は、新型コロナウィルス感染症等による環境変化においても、モノづくりを止めずに安定供給を守り、同時に人は緊急対応等に集中することを可能にする。東芝は、新型コロナウィルス感染症拡大防止のための緊急事態宣言(2020年4月)を受け、保守や社会活動の維持に必要な業務等を維持しつつ、基本的には製造現場を含めて出社制限をかけたが特に混乱はない。これには、人と同等以上の判断が可能なAI技術等もいちはやく実用化し、生産ラインの自動化を進めていることが大きく影響している。今後、人と機械の役割分担をさらに加速する研究を、二人の若手エンジニアに聞いた。
「工場の製造ラインで不良品を見つけて除外する検査工程において、視覚など人間の感覚に頼って製品の品質を判定する『官能検査』をAIに担わせることで、常に同じ基準で検査をし、見逃しも無くそうとしています。また、官能検査の現場でも働き手が不足していて、熟練者の技をどう継承するかが課題です。そこで、AIの深層学習を活用して、匠の暗黙知を機械に実装させることを研究しています。貴重な人材は、機械が検出した不良品の分析や、品質の安定化に向けた改善策やその運用を練ることに集中してほしいと思っています」
そう語るのは、チームで研究を進めている、株式会社東芝 生産技術センターの廣瀬佑介氏だ。

株式会社東芝 生産技術センター 製造プロセス・検査技術領域 光学技術研究部
研究主務 廣瀬 佑介氏
人間が行う官能検査は、人によってスキルや感覚が異なるため、どうしても良品・不良品の判定基準にぶれが生じる。特に溶接や成型などの加工では、熟練者でないと出来ばえの良し悪しを判定することが難しい。そこで、熟練の技術者たちが良品と判定した加工品の画像データから、基準となる良品モデルを抽出したAIを使うことで、ぶれの少ない安定した検査を実現できるという。だが、この良品モデルを作成するためのデータもやみくもに収集するだけではうまく行かない。なぜなら、加工品の形状や外観は、加工に使用した装置の個体ごとに微妙に異なったり、材料のロットの違いによる影響を受けたりして、複雑なバラツキを持つからだ。組み立て品であれば良品の外観はどれもよく似ており、平均的な外観そのものが良品モデルとなるが、加工品では単純に全ての製品の外観の平均をとるだけでは意味のあるモデルにならない。廣瀬氏のチームはこの問題を解決するため、様々な条件での良品データを網羅的に収集して、それに深層学習を適用することによって、加工品でも良品モデルを適切に構築できるように研究中だ。
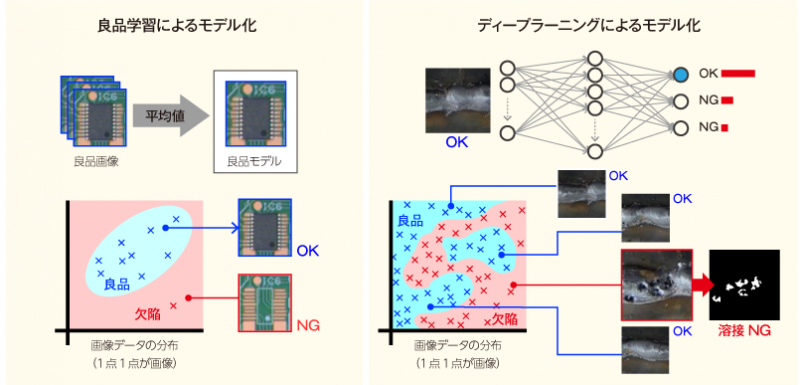
画像データ分布に応じた良品のモデル化
このデータ収集で、東芝のモノづくりの歴史が生きた。東芝の熟練の技術者は、この機械、この材料、この条件なら、こういう出来ばえで加工できる、ということを肌感覚で知っている。廣瀬氏たちチームメンバーは、何度も工場に足を運んで技術者にヒアリングを重ねて、泥臭く必要なデータを集めた。また、安定して良質な画像を撮影するためには「製造ラインのどの場所で、どういう条件で撮影すれば良いのか?」といったノウハウも、東芝のモノづくりの実績の中で培われたという。そして、AIが導き出した良品モデルが、本当に適切な加工品か否かを、技術者たちと丁寧に摺り合わせて確認していった。
さらに、廣瀬氏たちのチームは、深層学習を使う際に生じるブラックボックスという課題も克服しようとしている。深層学習を用いたアプローチでは、入力された良品画像のデータを何層も積み上げられたネットワークに通すことによって、良品の特徴を自動的に学習する。そのため、「なぜ、これが良品・不良品と判断されたのか」という検査結果の説明が難しく、使う人にとっては根拠不明(ブラックボックス)になってしまう。廣瀬氏たちは、深層学習が判断の際に画像のどこに注目したかを可視化する技術を応用することでAIの説明力を上げ、このソリューションを活用する人たちの納得感を高めようとしている。
欠陥品を効率的かつ安定的に検出できれば、企業の生産性が上がるだけでなく、製品出荷後のクレームや、さらには欠陥製品の回収・修理(リコール)など問題も解消することができる。それは、まさにAI技術を活用したモノづくりのイノベーションといえるだろう。
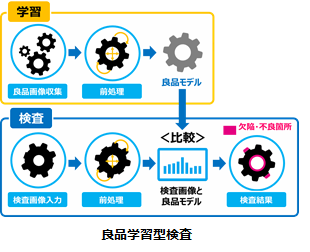
自らが生むデータで、自動最適化する溶接装置
製造業において溶接は、熟練技術者による匠の技が求められる生産工程の一つだ。彼らは、視覚、聴覚、感触を用いて目の前の溶接状態を把握し、加工条件を細かく調節している。しかしながら、人口減少による働き手の不足、熟練者を直ぐには育成できないといった理由から熟練者への身体的な負荷が大きく、工期が匠のスケジュールに依存してしまい、場合によっては遅延することもある。
この溶接をロボットに行わせ、最適な条件で溶接を制御しようと研究しているのが、株式会社東芝 生産技術センターの坂井哲男氏だ。
「2011年に始まったドイツのインダストリー4.0では、自動制御や、機器・システムの相互接続といったことを課題としています。東芝では2000年からデジタルマニュファクチャリングというITを最大活用した生産のコンセプトを掲げ、モノづくりの革新を続けてきました。こういった流れのなかで、自動化が遅れている溶接技術に対して、AI技術を活用することでロボットが自律して溶接を行えるように研究を進めています。その結果、加工に費やしていた人件費を節減でき、人が次の価値を生む技術やシステムの開発に注力できるので、企業価値の持続的な向上につながります。また、高度な製造技術を持つことで、豊かな社会の実現に貢献できると思っています」

株式会社東芝 生産技術センター 製造プロセス・検査技術領域 光学技術研究部
研究主務 坂井 哲男氏
坂井氏の研究の構想は、レーザ溶接を例に挙げると次の通りだ。まず、ロボットがどのように溶接をしているのか分かるように加工点を明瞭に撮像し、リアルタイムで画像データを収集する。それら画像に対して、レーザ照射箇所や、レーザの熱で金属が溶けている箇所といった特徴量のデータをAIで抽出する。抽出されたデータはサイバー空間(Cyber space)へと転送され、シミュレーションや実験により、事前に構築された溶接状態データベースと照合される。そして、次の溶接箇所の状態に合わせて、最適なレーザ溶接の条件が選ばれる。その最適条件を現実空間(Physical space)のロボットにフィードバックすることで、適切な溶接が行われる。このような一連のプロセスを何度も繰り返すことで、常に最適なレーザ溶接条件を保てるような自律型の溶接システムを開発している。
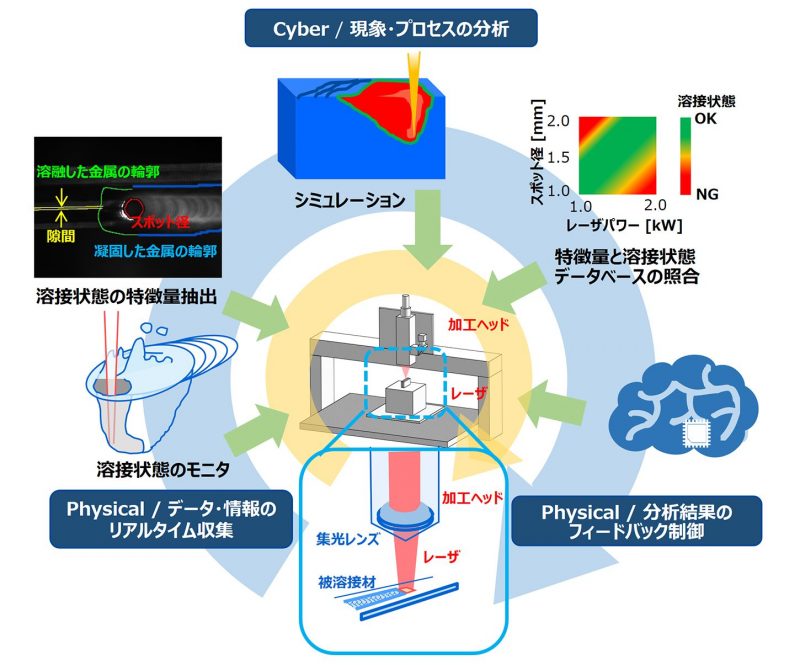
レーザ溶接のCyber-Physical Systems化の構成例
坂井氏の研究は、東芝の溶接分野では初めての挑戦だった。最初の頃は仲間づくりから始まり、現場の溶接士たちをマネジメントする事業部の担当者と、研究所の若手メンバーの小さなチームで研究に着手した。坂井氏をこの研究へ駆り立てたのは、「東芝が継続的な投資によって脈々と積み上げてきたモノづくりの知見が、50年以上にわたるAI研究で培われたデジタルな分析技術と結びつくことで、大きな価値を生むはずだ」という信念だ。モノづくりに対してAIによる情報や知識を導入することは、日本の製造業の位置づけを上げることにもつながるという思いでもあり、研究の歩みは緩まなかった。その後、研究成果が製造工程へ反映される見込みが得られ、多部門と連携する研究体制へ移行していった。実際に、溶接状態の特徴量を抽出するAI技術の開発は、前述の廣瀬氏たちのチームが担い、溶接状態のシミュレーションは、この研究のために若手エンジニアが独自開発した。一人のエンジニアによる変革への情熱が仲間たちの心に火をつけて、知恵を結集することで新しい価値をともに生み出しているのである。
坂井氏の研究のように、現実世界のデータをサイバー空間へ転送・分析して、活用しやすい情報や知識として現実世界にフィードバックすることで価値を創造する仕組みをCyber-Physical Systems(CPS)という。東芝はCPSテクノロジーを駆使してインフラサービスカンパニーを目指しており、モノづくりの現場を含め様々な領域で社会実装を進めている。廣瀬氏、坂井氏たちのような東芝のエンジニアは、常に社会実装を見据えて技術を磨いているのだ。
社会実装の実例として、世界最大手の自動車プレス部品メーカーであるGestamp社との実証実験がある。そこでは、東芝のモノづくりの知見、分析技術を生かして、Gestamp社のドイツ工場で、カメラ画像データによる表面検査とAEセンサー*データによる内部検査を組み合わせたソリューションにより、高度な溶接検査の実現を目指している。
*AEセンサー:高周波数帯の音波を検出し、物体の破壊や変形をとらえる。
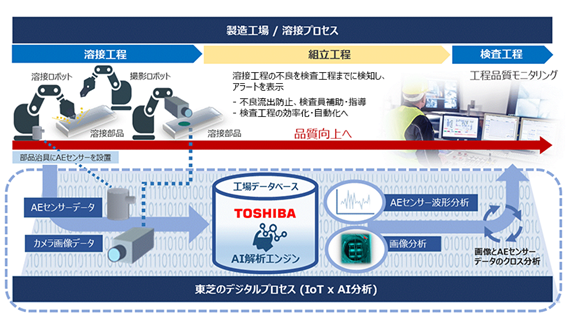
東芝とGestamp社の取り組み概要
AI技術の活用により官能検査やレーザ溶接が自動化されることで、人間は人にしかできない業務に集中できるようになり、新しい価値を生み出せる。これらは、東芝が50年以上にわたって積み重ねたAI研究と、140年を超えるモノづくりの経験と実績が組み合わさって生まれるものだ。その成果は、生産革新といったモノづくりに留まらず、カラオケやテレビなどの身近な暮らし、そして医療など様々なジャンルに展開されている。東芝のAI技術は、東芝グループの様々な知見と組み合わされることで、これからも新しい未来を創造していくだろう。