自律移動ロボット「AMR」と見る未来 ~労働力減少の課題解決を目指して
2021/12/03 Toshiba Clip編集部
この記事の要点は...
- 労働人口が減少する中、物流・製造現場で進む「次の」自動化!?
- 自分の位置と、向かう先が分かる自律搬送ロボットが実装間近?
- レーザー、メカナムホイールなど先進技術に加わる、ものづくりのDNA
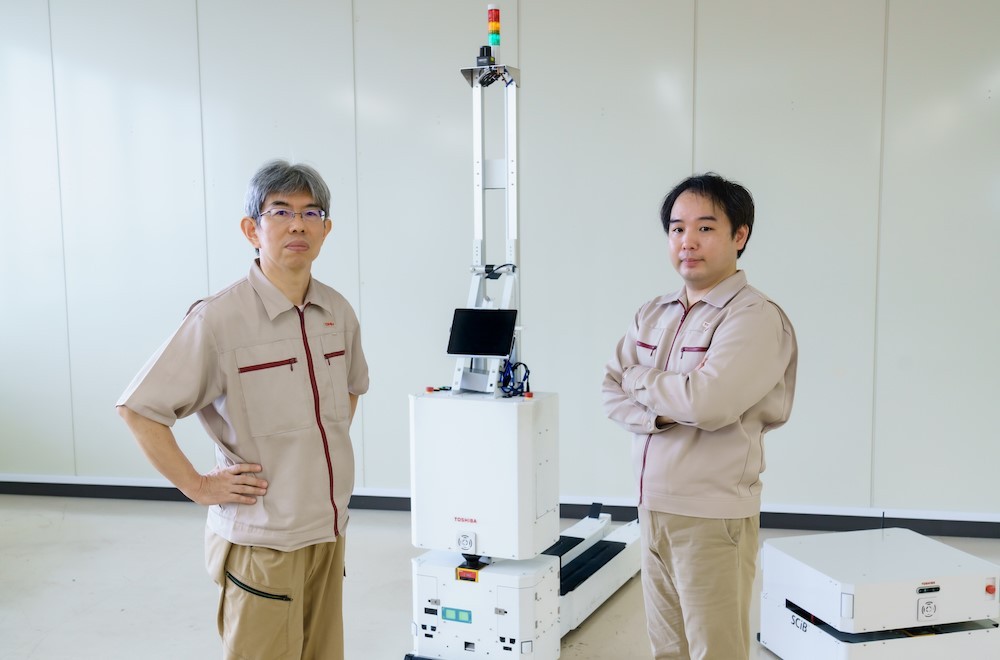
コロナ禍による巣ごもり需要の拡大により、EC※市場は拡大の一途だ。一方で、少子高齢化による人手不足は深刻さを増し、物流インフラにも大きな負荷がかかっている。もはや人間による手さばき、ベルトコンベアー程度の機械化で物流現場を回すのは困難だ。今、物流業界では倉庫情報管理システムなどが実用化され、「自動化」「生産性の向上」を軸に研究・開発が進む。その一つがロボットの活用である。
※Electronic Commerce:インターネットにおける、ものやサービスなどの売買
東芝は人間の「運ぶ」工程を自動化する「自律搬送ロボット」を開発し、グループ内での適用を開始した。これは、物流現場のニーズに応え、さらに大量生産の製造ラインでの活躍も視野に入れるものだ。プロジェクトを進める生産技術センター RPJ(ロボット製品化技術推進プロジェクトチーム)の森明慧氏、寺田明人氏に、「自律搬送ロボット」の開発背景から現在、そして実装への期待を語ってもらう。
株式会社東芝 生産技術センター ロボット製品化技術推進プロジェクトチーム 上席研究員 森 明慧氏
「ガイド付き自動」から「自律」へ ――次世代移動ロボット・AMRが現場を変える
「物流・製造現場では、膨大な物量の運搬や、高所作業など人間の作業をロボットに置き換えることが求められています。労働人口が減少する中、現場の改善は今すぐに、という思いがありました。コロナ禍でさらに負荷がかかる中、ロボット技術で社会に貢献できれば――そんな思いが、私たちを支えています」
そう開発の経緯を語るのは、生産技術センターで開発リーダーとしてプロジェクトを推進する森氏。従来、製造・物流現場では人間が荷物を台車などで運んでいた。自動化やロボット導入が進む製造現場でさえ、「運ぶ」という作業は人力に頼ることが多い。「運ぶ」を自動化できないか――そのニーズに応えるべく、多くの企業がAGV(Automated Guided Vehicle:無人搬送車)の開発・競争に参入している。
AGVは荷物を所定の位置へと運ぶべく、床の磁気テープを追跡したり、床や壁に設置されたマーカーを読み取ったりして、決められた手順で自動走行する。そのため、経路を変更するにはテープやマーカーなどのガイドを設置し直す必要があり、柔軟な運用には限界がある。そこで注目されているのが、ガイドなしに自律的に動いて荷物を運ぶAMR(Autonomous Mobile Robot:自律移動ロボット)だ。物流・製造の現場では、どのようなニーズから「自律」ロボットが待望されているのか。
「品物の収納や取り出しが自動化された倉庫など、無人や全自動で稼働するような状況ではAGVが適しています。一方、人とロボットが作業を分担し、作業を徐々に変化させるなど、ゆるやかに自動化が進むのが製造・物流の現場です。状況に応じて柔軟に移動・搬送し、人と協働して力を発揮する――そんなAMRを思い描きながら開発、研究に取り組んでいます」(森氏)
従来の自動搬送台車(AGV)と違い、自律移動ロボット(AMR)に求められる機能
AMRは自らが「どこにいるかの位置」を認識し、「向かうべき先」へ自律移動する。位置認識にはカメラ方式とレーザー方式があり、本プロジェクトでは水平スキャンを行う走査型のレーザー距離センサーを採用した。これは、レーザーで壁や柱などを読み取って地図を作成し、その地図中で自らの位置を認識するものだ。
「カメラは前方を面で捉えることができますが、視野角は限られます。一方、レーザーだと水平方向に限られますが270度の視野を持ち、周囲の環境を広く捉えられます。さらに、レーザー距離センサーのデータは効率よく計算できCPUへの負荷を抑えられるので、複数のセンサーを同時に使ったより広い視野を処理することも可能です」
株式会社東芝 生産技術センター ロボット製品化技術推進プロジェクトチーム 上席研究員 寺田 明人氏
目的の場所に到達した後、停止位置の調整誤差は±10mm。ここでは、カメラを使用して高精度に位置を決める。移動と停止──目的に応じてレーザーとカメラを使い分け、さらに長年のロボット開発で培ってきたデータ処理がバックアップ。ハードとソフトの融合により、現場ニーズを満たすAMRを実現している。それだけではない、他社に先駆けて実装した新機構もある。ハードウェア開発を担当した寺田氏に聞こう。
「ちょっと斜めに動ける」ことの大きな価値
「足回りに採用したのがメカナムホイール。体勢を変えずに、前後左右、斜めと全方向に移動できる特殊車輪です。物流現場で使われるAGVは2輪駆動が一般的ですが、台車などの所定位置へドッキングする際は何回も切り返しが必要です。全方向に動いて位置合わせできるメカナムホイール搭載ロボットなら、無駄な時間を省いて生産性を向上できます。『ちょっと斜めに動ける』ことが、どれだけ現場では大きいか。製造現場への適用など、さらなる広がりも視野にあります」(寺田氏)
全方向への移動を可能にするメカナムホイール
AMRを支える仕組みにも余念がない。バッテリーには長寿命で急速充電が可能な二次電池SCiB™を搭載して短い充電時間により、高い稼働率を支えている。また、複雑な物流・製造現場を想定したフレキシブルな運行管理システムを開発。複数台でも効率良く走らせる仕組みを整えた。
「ロボットの稼働時間を伸ばすことだけを考えれば多くの電池を積めばいいのですが、東芝のSCiB™なら鉛蓄電池の1/8時間程度で急速充電でき、繰り返し充電しても劣化が少ない特長があります。こまめな充電で稼働し続ければ、物流や製造の現場で頼もしい存在になるでしょう。
また、ロボットの台数が増えても混乱を来さない。これは、運行管理システムの同時制御、柔軟さによるものです。さらにログを検証すると、ロボットの待ち時間や滞留しがちな場所を可視化できます。さらなる導線の改善、ロボットの最適な運用シフトを設定できるでしょう」(森氏)
連携して効率よく稼働するための運行管理システム
現場の声から価値が生まれる――自律移動ロボットを生んだDNA
タフな現場で運用されるAMRに求められるのは、どんな環境でも安定して稼働することだ。メンバーは何度も現場に足を運び、多くの「声」を集めた。試行錯誤で精度、柔軟性を高める中、PoC(概念実証)を進める物流現場で、「カゴ車の下にAMRが潜り込んで、安全に運んでほしい」というニーズをつかんだ。
カゴ車が倒れないよう、その車輪が接地した状態でAMRが運ぶ「半荷重搬送機能」
「実験室ではスムーズに動いても、人や荷物、機材が並ぶ実際の現場では想定外の改良ポイントが見つかります。新しい技術への気づき、発見は現場でしか得られません。かつてテレビ事業に携わっていたとき、私たちは顧客や販売店の『声』から次の価値を生んでいました。今回も同じです、これは技術者として受け継いだDNAですね」(森氏)
この改良により最大で600kgの重量にも対応できるようになったという。また、先に挙げた「レーザー距離センサー」「メカナムホイール」「SCiB™」「柔軟な運行管理システム」といったAMRの長所は、いずれも「現場の声」に基づき、「現場の生産性向上」に直結するものだ。根底にあるのは、ものづくりのDNA「現場で使われ、役立つものを届けたい」であり、東芝の技術者、研究者に共通のものだ。
「AMRの開発は移動ロボットの要素技術の研究を行ってきた研究開発センターと、生産現場の部品搬送の自動化を目指してきた生産技術センターが一緒になって開発に取り組みました。このとき、DNAを共有しているので建設的に議論できましたし、現場に広く、深く目を配ることで最適なソリューションを提案する共通ゴールはぶれませんでした」(寺田氏)
145年に及ぶ東芝グループのものづくりの原点には、創業者の一人「からくり儀右衛門」こと田中久重が手がけた「弓曳童子」、つまり人間の動きを模した原初ロボットがあった。AMRの開発には制御技術やセンシング、メカトロニクスに至るまで、ロボットや自動化機器の開発で蓄積してきた技術資産、そしてDNAが生かされている。人とロボットが協働して新たな価値を生み、社会課題の解決にも寄与していく――AMRは、2020年代のニーズに応えるロボットの現在進行形なのである。