世界シェア50%*!東芝「セラミックスボール」の強さとは? ~AI品質検査でモビリティ電動化に貢献
2023/04/24 Toshiba Clip編集部
この記事の要点は...
- 宇宙船、風力発電、電気自動車……広がるセラミックスボールの活用
- AIの東芝だから実現できた、AI品質検査の開発・実装の裏側とは?
- MLOps活用でAI運用コストが削減可能に、カーボンニュートラル貢献へ加速!
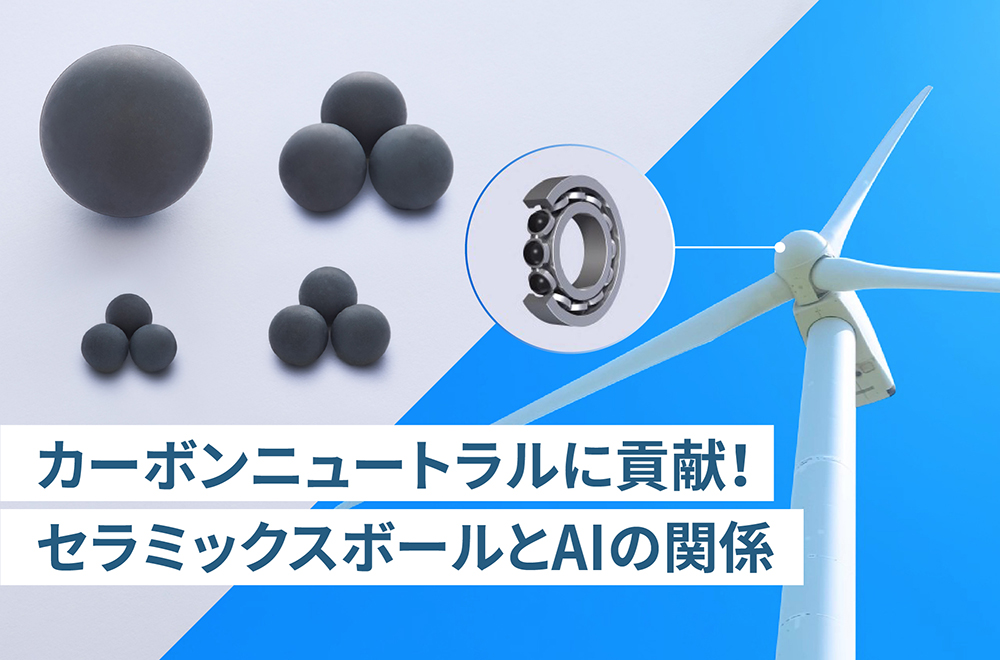
カーボンニュートラル達成の鍵を握る1つにEV(電気自動車)の普及があり、世界で販売が伸びている。EVの重要な部品がモーターに搭載される軸受、いわゆる「ベアリング」だが、普通のベアリングでは「電食」という現象が発生して故障につながる。その課題を解決したのが、「セラミックスボール」を活用したベアリングだ。
出典:経済産業省「モビリティの構造変化と2030年以降に向けた自動車政策の方向性に関する検討会 参考資料」
東芝マテリアルのセラミックスボールは、研磨メーカーに供給され、ベアリングメーカーを経て、欧米の自動車メーカーを中心に活用されている。それを可能にしているのが、世界50%*というシェアに表れるノウハウと高い技術、そしてAIによる高度な品質検査だ。東芝が進める、AIを活用したセラミックスボールの品質検査に迫った。
特許と実績を誇る、東芝のセラミックスボール
アクセルを踏み込んでも自動車独特のエンジン音はない。それなのにスーッと力強く加速する。EVのハンドルを初めて握ると、ガソリン車とは異なる感触に驚きと未来を感じることだろう。この特徴的な挙動はモーターが生んでいる。そこで重要な役割を担う部品がベアリングだ。
「ベアリングは、機械の中にある軸をなめらかに回転させる部品です。内輪・ボール・外輪で構成されています」と教えてくれたのは、東芝マテリアルの山田勝彦氏だ。一般的に、内輪・ボール・外輪には金属が使われるが、高出力が求められるEVのモーターでは電食という現象が起き、課題となっている。
ベアリングの模式図
「ベアリングは内輪に軸が密着し、外輪と内輪の間にボールが入っています。このボールによって、軸が滑らかに回転します。ボールは内外の輪と常に接触すべきなのですが、どうしても僅かな隙間ができてしまう。その隙間に電気が通ると放電による火花が発生し、ボールが傷ついてしまう、これが電食です。特に高出力のモーターは、軸の回転が速く電食が発生しやすくなります」(山田氏)
東芝マテリアル株式会社 構造用FC製造部 構造用FC製造技術担当 グループ長 山田 勝彦氏
ベアリングは、一度組み込めば簡単には取り替えられない。米国では、EVに採用するベアリングには長距離走行に耐える品質が求められる。高品質の製品がEV普及を促し、カーボンニュートラルに貢献するのだが、電食が発生するとそれが叶わない。その課題を解決するのが、セラミックスボールを使ったベアリングだ。
なぜ、セラミックスボールでは電食が起こらないのか。山田氏は「セラミックスは電気を通さない絶縁体だから」と説明する。他にもセラミックスボールは、金属製の半分以下の重量、高い耐熱性、酸やアルカリによる腐食や錆への強さといった特長も併せもつという。
東芝は、古くからセラミックスボールを製造してきた。それは1974年、セラミックスボールの原料となる窒化ケイ素の特許取得に遡る。アルミナなど様々な種類がある中、東芝は、軽く強度に優れる窒化ケイ素にこだわった。
「1985年に工作機械のベアリングに採用されて以降、1995年にスペースシャトルのターボポンプに、2008年に風力発電機に採用されました。今では、航空機エンジンや医療機器などにも使われています」(山田氏)
東芝のセラミックスボール
EVモーターに使われるようになったのは2014年、カーボンニュートラルに向けて需要が急激に伸びているという。欧米系メーカーを中心に供給し、東芝が選ばれる理由は、実績と技術力に裏打ちされた信頼だ。セラミックスボールにおけるシェアは今や約50%*に至る。
「AIの東芝」だから実現した、AI品質検査の裏側
需要が増えれば、当然、品質検査も多忙を極める。当初、セラミックスボールの検査は、東芝の社内試験に合格した検査員が目視で行っていた。しかし、熟練者の高齢化や昨今の人手不足もあり、検査の効率化が喫緊の課題になる。そこで導入されたのが自動検査装置だったが…。
これは上手くいかなかった。山田氏は、「自動検査装置は、装置が自ら撮影した画像を判断し、不良品をはじく仕組み。しかし、焼きむらの色味を判定できませんでした」と悔しさをにじませる。セラミックス製造では、素材を高温で焼く工程がある。熟練の検査員は、焼き上がりの微妙な濃淡で小さな穴などを経験的に判別するが、機械にはそれが難しかった。
「今だから言いますが、正直なところ諦めていました。この装置はお蔵入りです」と苦笑する山田氏。救いの手を差し伸べたのは、東芝 生産技術センターだ。同センターの鷲谷泰佑氏は、当時をこう語る。
「当時、生産や検査の自動化が推進されていました。様々な現場に足を運ぶ中、山田さんから自動検査装置に読ませる画像を見せてもらいました。それを見た瞬間、AIの深層学習と相性がいいと、直感的に分かりました」(鷲谷氏)
株式会社 東芝 生産技術センター 製造プロセス・検査技術領域 光学・検査技術研究部 スペシャリスト 鷲谷 泰佑氏
早速、AIを活用した品質検査を提案。お蔵入りになった自動検査装置が、別の使われ方をした瞬間だ。
「生産技術センターは現場密着型。現場で使える装置や技術を最大限に活用し、よりよいモノづくりに貢献します。ボールを回転させながら撮影する自動検査装置を活用できたので、画像が良品かどうかを判定するAIさえ組み立てられれば、十分いけると判断しました」(鷲谷氏)
セラミックスボールを3方向の角度で回転させながら、ラインセンサで撮影
AIには典型的な深層学習のアルゴリズムを採用。鷲谷氏は「難しかったのは、アルゴリズム開発よりも、もっと泥臭い部分だった」と、適用段階で性能を発揮しきれなかったことを振り返る。
「AIが学習するデータは人が用意します。そのデータに、ある人が見たらNGで、別の人が見たらOKといった曖昧さが含まれていたのです。そのままAIが学習したことで、判定に曖昧さが混じり、満足いく精度を達成できませんでした。
結局、怪しい画像は学習に回さない、という泥臭い方法で精度を上げました。そして、ある程度使えるようになったら現場に投入し、AIの評価を人間が確認し、アルゴリズムを修正していきました。約1年半にわたり学習を続け、徐々に精度を上げる地道な作業でした」(鷲谷氏)
AIと聞くと魔法の杖を想像するだろう。だが現場に適応させるには、適切な学習用データや、現場密着の技術者による調整が欠かせない。数多くのAI特許を持つ東芝だからこそ、品質検査AIを実現できたとも言えるだろう。
MLOpsの活用で、検査期間と人件費を大幅に短縮
無事、品質検査に導入されたAI。話はここで終わらず、むしろここがスタート地点だった。なぜなら、AIの品質検査は、セラミックスボールへの照明のあたり方、材料の変更など前提条件が微妙に変わると、精度が変化するからだ。こうした変化を考慮してAIを調整し、精度を保つ必要がある。つまり、運用しつつメンテナンスするようなものだ。そこで登場するのが「MLOps」である。
MLOpsは、Machine Learning(機械学習)とOperations(運用)を組み合わせた言葉。東芝 デジタル・イノベーション・テクノロジー・センターでMLOpsを開発する小畠知也氏は、「AIの精度を確認して、学習を更新させるなど、ライフサイクル全般を自動化します」と語る。
株式会社東芝 デジタル・イノベーション・テクノロジーセンター 技術開発室 サービスプラットフォーム開発部
スペシャリスト 小畠 知也氏
「セラミックスボールは、材料の変化などで1年半の周期で微妙に変化する。その品質検査に対応するには、AI自体を更新し続ける必要があります。MLOpsは、その作業を自動化しています」(小畠氏)
先ほど、鷲谷氏は「泥臭い方法で精度を上げた」と発言したが、「最初からMLOpsを使えば、短縮できただろう」と語る。実は、MLOpsの現場適用は、セラミックスボールの品質検査AIの開発時に間に合わず、運用してからの適用となったそうだ。
MLOpsの仕組み
「今後、AI全般において、MLOpsを活用することで開発の短縮や精度の維持・向上、運用の省人化が見込めます。MLOpsを手掛けるチームは小回りが効き、東芝自体もどんどん決断と実行を早め、横の連携も活発です。その強みを生かして、東芝のあらゆる領域にMLOpsを導入していきます」(小畠氏)
かくして、無事、AIを活用したセラミックスボールの品質検査は軌道に乗った。そして、人手不足という課題に対して、目に見える効果を発揮している。
「検査に費やしていた時間を大幅に削減できました。セラミックスボールは、金属製に比べると高価です。強みが多いのに、鉄製から置き換わらない理由はそこにあります。品質検査AIでコストを抑えれば、製品の価格を抑えられます」(山田氏)
冒頭で触れたように、カーボンニュートラル実現に向け、EVの普及が加速度的に進んでいる。それは、セラミックスボールの需要の更なる増加を意味する。東芝は製造棟を新設し、生産能力を2021年度比150%に増強する予定だ。
最後に、今回のプロジェクトを通じて、3人が感じたことを語ってもらった。
「セラミックスボールの生産拡大により、品質検査の役割も重要になります。いくら熟練者でも判断に差が生まれるし、その熟練者も減っている。AIなら同じ基準で検査でき、省人化にもなります。東芝だけでなく、お客様にも大きな価値を提供できるのです」(山田氏)
「生産技術センターは、東芝全体の研究部門として様々な現場で自動化を手掛けています。私たちが横串を通して、今回のように一つの現場で得られた知見を別の現場に展開していきます」(鷲谷氏)
「東芝は、研究、開発、生産それぞれで一流の技術を持っています。強みを120%生かし、東芝だからできることを、より多くより早く実現していくのが目標です。MLOpsはそのためのプラットフォーム。東芝の最先端のAIを様々な事業につなげ、お客様や社会に貢献したいですね」(小畠氏)