高品質半導体の製造を支える、見えない相手との戦い
2020/06/03 Toshiba Clip編集部
この記事の要点は...
- クリーンルームの保守・保全は見えない相手との戦い
- 故障原因の徹底究明で、修理費を大幅削減!
- 無ければ作る!で乗り越えてきたものとは
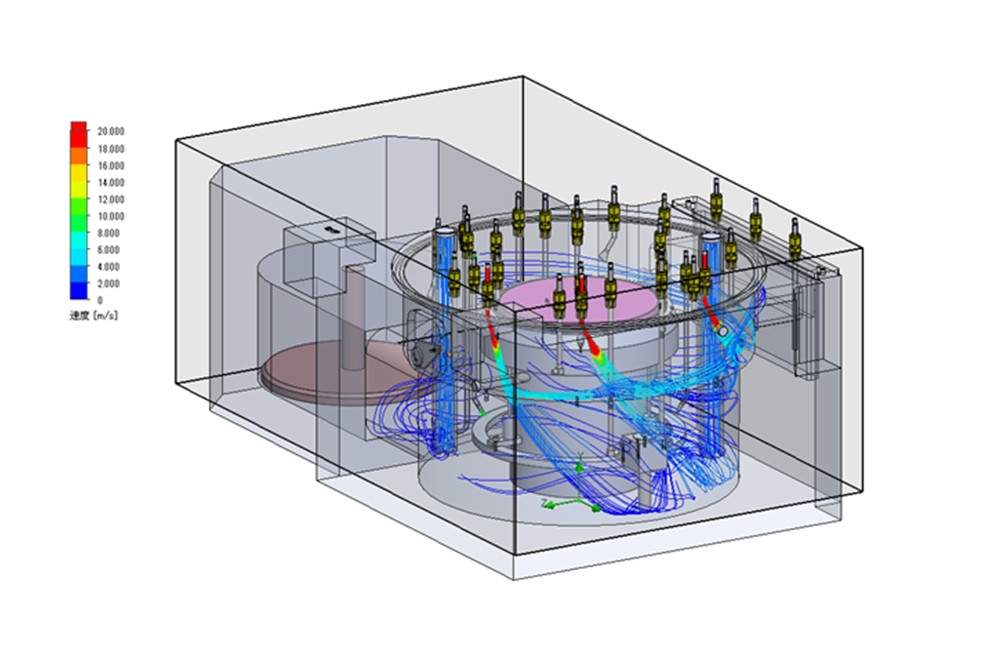
東芝グループの半導体製造を担う株式会社ジャパンセミコンダクター大分事業所では、主に自動車などに使われる半導体を製造しており、特に高い品質が求められている。
長年にわたって高品質の半導体を製造してきた同社が、どのようにして高い品質を維持してきたのか。半導体製造現場を支える保守・保全活動に従事する担当者たちの活躍に迫ってみよう。
高品質を維持するために大切なこと
前編の半導体ができるまでの流れでもご紹介した通り、目に見えないほど小さなダストが品質の低下に直結するため、半導体は空気が管理されたクリーンルームの中で製造されている。クリーンルームの清浄度は、気圧差や防塵服の着用など、外部からのダスト侵入を防ぐ様々な取り組みによって保たれているが、ときにクリーンルーム内部でダストが発生することもあるという。
「半導体の製造過程で、ダストの原因となるものが生まれます。こうしたダストも品質に影響しますので、専用の器具を使った定期的な清掃が必要なのです」
そう話すのは、ジャパンセミコンダクター大分事業所製造部の岡崎裕一氏だ。
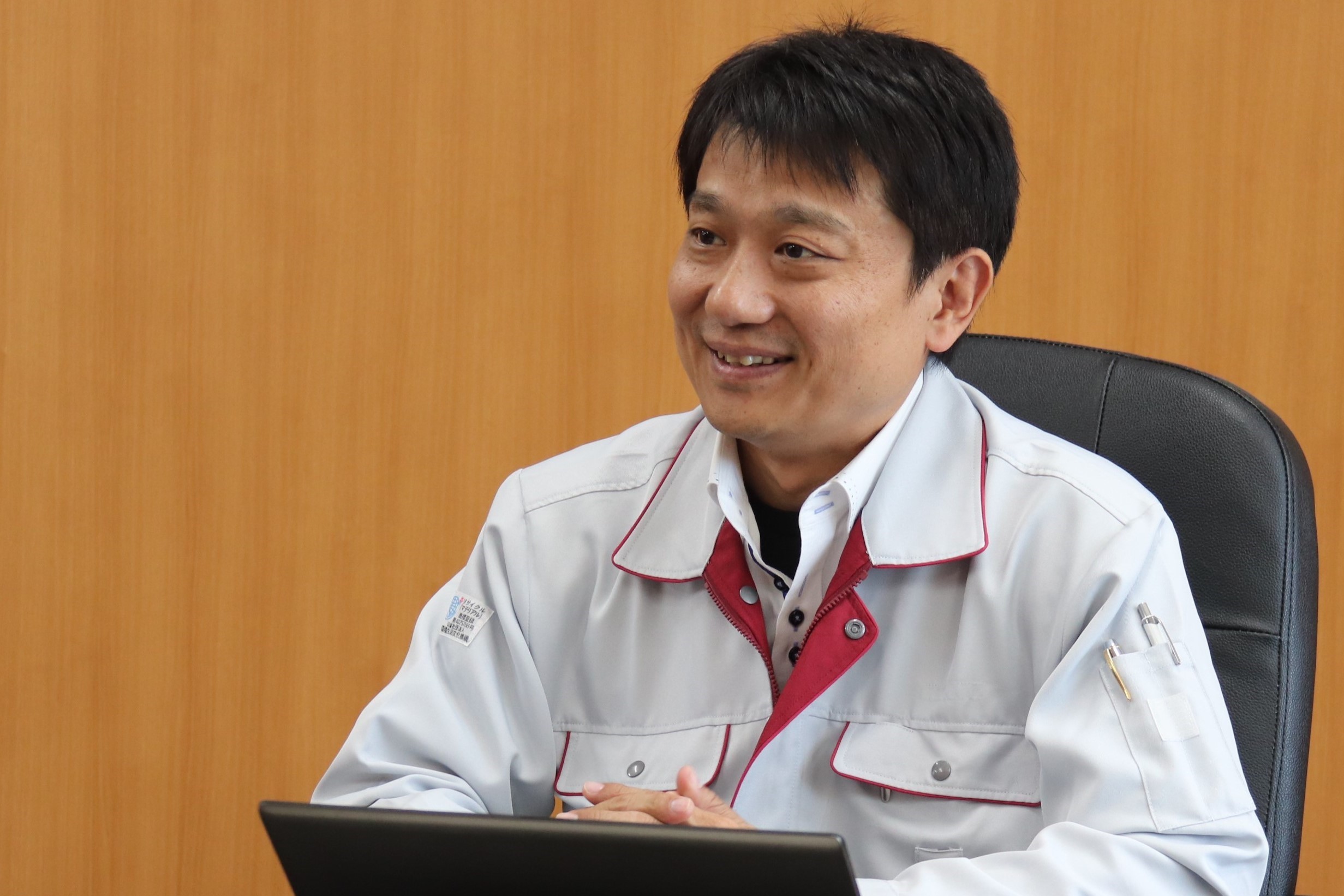
【図1 株式会社ジャパンセミコンダクター 大分事業所 製造部 製造長 岡崎裕一氏】
半導体は、ウエハー上に成膜を行って、それをエッチングなどで削り取るような作業などが繰り返されて作られる。この際取り除かれる膜などが新たなダストの原因となるのだ。
「例えば、チャンバーと呼ばれる反応容器の中には、どうしても膜のくずが残ってしまいます。これも不良品の原因となりますので、定期的なチャンバー内の清掃が欠かせないのです」(岡崎氏)
数年前までチャンバーの清掃は、熟練の作業員による手作業で行われていたという。メチルアルコールを含ませた布で拭いてから、残ったダストを高圧エアガンで吹き、バキュームで吸い取るという作業だ。
「チャンバー内のダストは肉眼では見えないため、経験と勘だけが頼りでした」(岡崎氏)
この手作業による清掃は、一台あたり120分もかかっていたという。また、作業員の習熟度によって洗浄結果にばらつきが生じるという問題も抱えていた。こうした課題を解決するために、チャンバー内の清掃を自動化するプランが持ち上がる。
「日々試行錯誤を繰り返す中で、チャンバー内の気圧を外より低くすると、効率良くダストを吸い取れることがわかりました」(岡崎氏)
「さらに、社内の装置技術部門に協力を依頼して、チャンバー内の気流シミュレーションを行うことで、エアガンのノズルの位置や角度の微調整を重ねました」(岡崎氏)
こうして、チャンバー内の自動清掃を行う器具、「オートシーケンシャルブロー」が誕生した。これによって、洗浄時間が120分から45分へと一気に短縮され、また、作業者は器具のセットとリセットを行うだけなので、作業者ごとの洗浄度のばらつき問題も解決されたのだ。
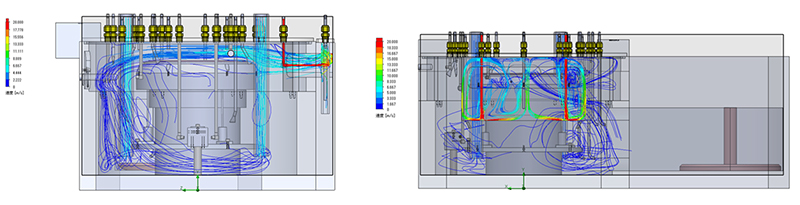
【図2 気流シミュレーションを行ってチャンバー内の空気の流れを可視化。目に見えない敵との戦いを制した】
「これに留まらず、エアガンのノズル形状を円形から扇形に変更し広角的に洗浄することで、洗浄時間をさらに30分にまで短縮できました」(岡崎氏)
実に、手作業による洗浄の4分の1にまで所要時間が短縮されたのだが、進化はこれだけではない。現在は新たに一度ブローした後、ダストの多かったエリアを次から集中的にブローすることにより、全体のダストの終息を早める自己診断・自動判定機能を追加しているという。
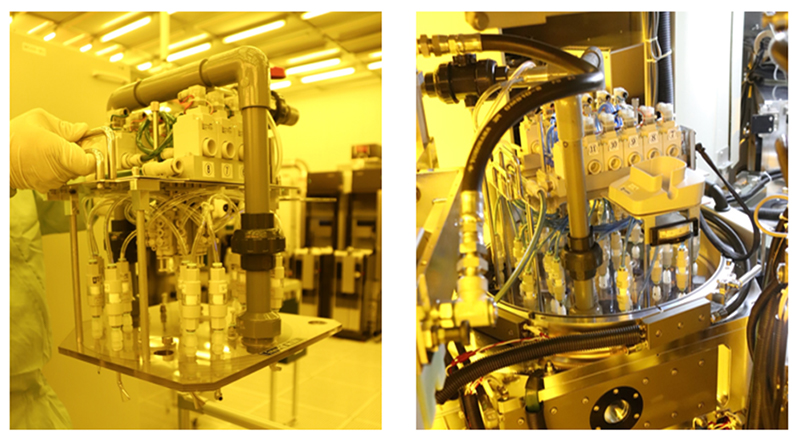
【図3 左:オートシーケンシャルブロー本体/右:チャンバーにセットされた状態】
攻めの保守・保全活動で目指すもの
ジャパンセミコンダクター大分事業所で、保守・保全活動を行う担当者は、総勢133名。スキルレベルによって、装置の定期的なメンテナンスを行うメンテマン(MM)、診断機材を使って定量的な修理を任されるマシンキーパー(MK)、そして、難易度の高い故障解析で真因を追究し予知・予防・改良保全を担うスペシャリストマシンキーパー(SMK)の3つの階層に分かれている。それぞれに求められる役割があるが、上の階層を目指してスキルアップするための育成カリキュラムも用意されている。
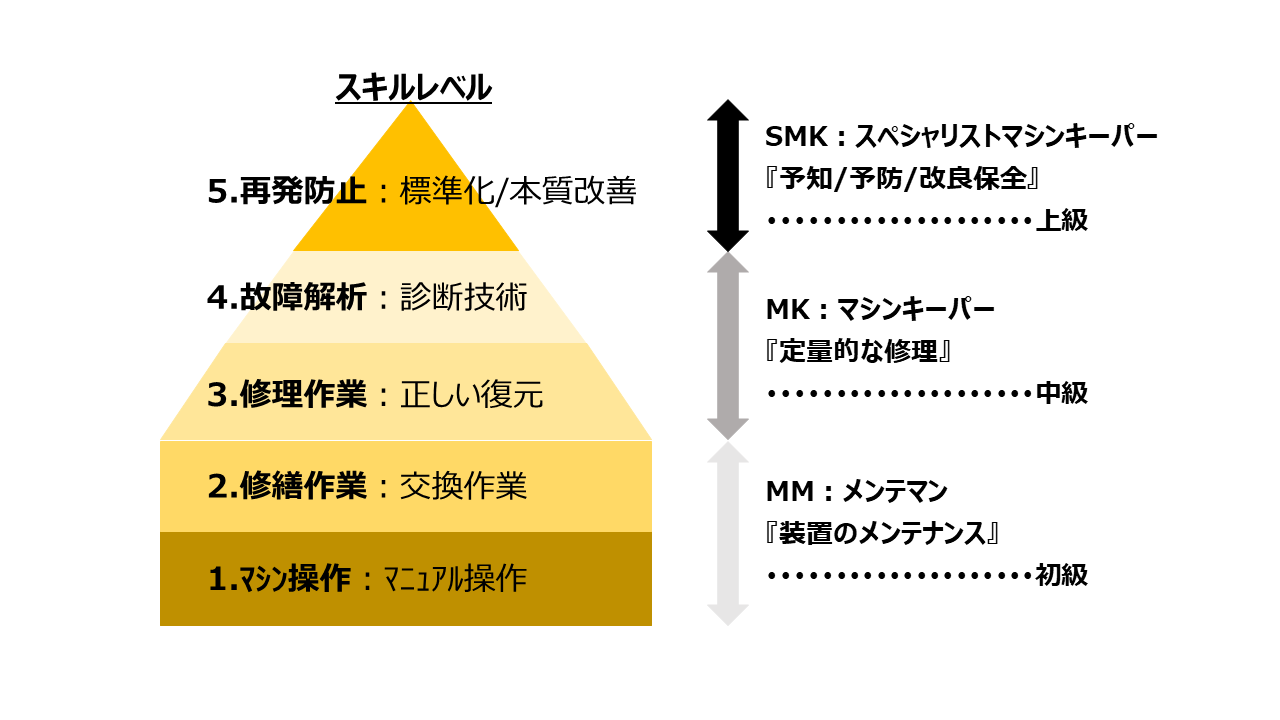
【図4 ジャパンセミコンダクター大分事業所の製造設備保守・保全体制】
「より高い技術を身につけて上のレベルを目指せる環境が、大きなモチベーションとなっています。最上位のSMK達は、常により高い目標をもって攻めの保守・保全を行っています」(岡崎氏)
製造ラインは、設備に何か問題が起こるとアラームが鳴り、処理が止まってしまう。すると、工程によっては製品の再処理が必要となるなど、最悪の場合は納期に影響が出てお客様に迷惑がかかってしまう可能性もある。そこで、高品質を維持しながら、製造ラインを順調に動かし続けるために、前述の133名からなる保守・保全担当者たちが、昼夜を問わず活動しているのだ。
「我々SMKには、通常の保守だけで終わらない、その先の二つの目標があります。一つが、故障原因の徹底究明です」
そう語るのは、ジャパンセミコンダクター大分事業所製造部の羽田智幸氏だ。
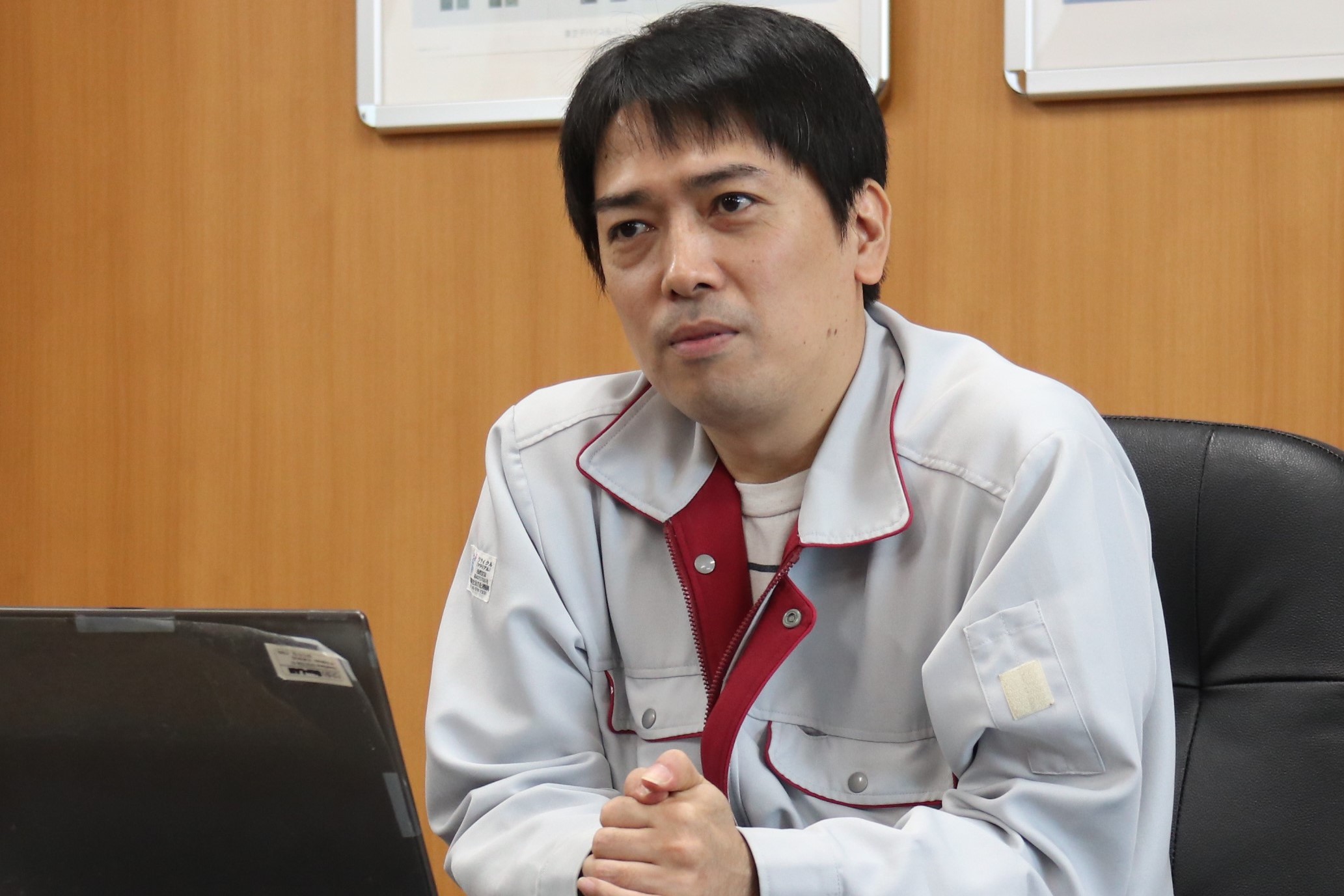
【図5 株式会社ジャパンセミコンダクター 大分事業所 製造部 羽田智幸氏】
通常、半導体の製造装置の修理は、壊れた個所を装置メーカーが販売するユニット単位で交換するケースがほとんどだ。これは製造ラインが止まる時間を最小限に抑えるためで、実際にはネジやコンデンサーが一つ壊れていただけだとしても、そこまで調べることなく、壊れた部品を含んだユニットが丸ごと交換される。
「でも、壊れたユニットをばらしてみると、本当は安くて小さな部品を交換すれば良いだけというケースがあるのです」(羽田氏)
こうした場合、装置メーカーから購入する交換用ユニットに比べて、驚くほど安く、早く修理が完了することも少なくないという。
「故障の真因を追究していくと、壊れやすい部品が見えてきます。それがわかれば、壊れないような使い方を検討したり、壊れにくい部品に変更したりできます。こうすることが、装置の寿命を延ばすことにもつながると考えています。我々のもう一つの目標は、今ある装置を30年後まで使い続けることなのです」(岡崎氏)
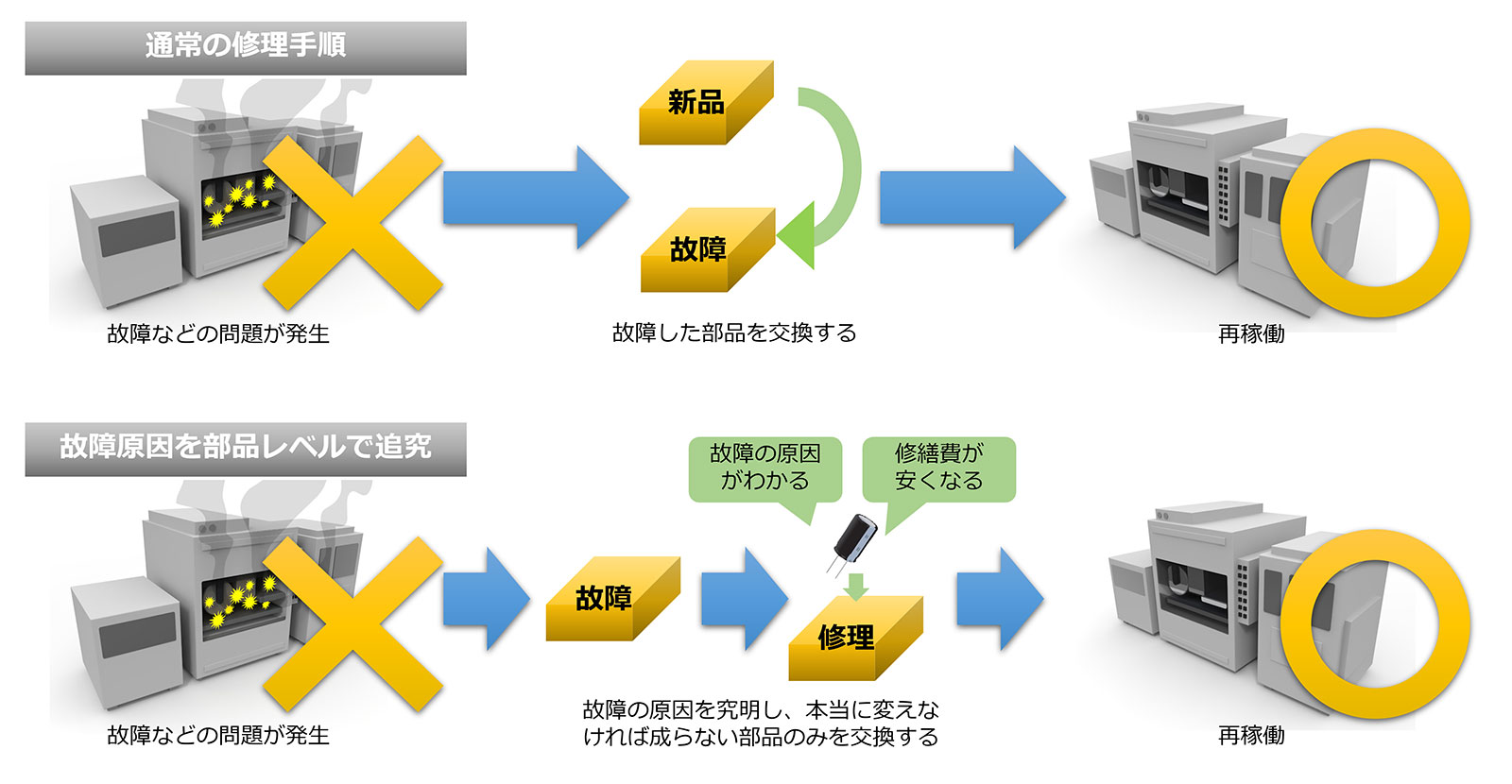
【図6 下がジャパンセミコンダクター大分事業所の取り組み。故障の真因を追究し、驚くほど安く、早く修理が完了することも】
このように徹底してトラブルの原因を究明することで、故障をゼロにしたり、半年に約1,000万円かかっていたある装置の修理費を10分の1に抑えることに成功したりした例もあるという。
「とにかく、徹底的にやってみる。その挑戦の先に、経費の節減や稼働率の向上があるのだと思います」(羽田氏)
また、こうした徹底究明や修理のためには、市販の器具だけでは足りないことがある。同社では、32種類の器具を使っているが、実に半分以上の18種類は、独自に開発したものだ。
「必要なものが無ければ、作ることにしています」(岡崎氏)
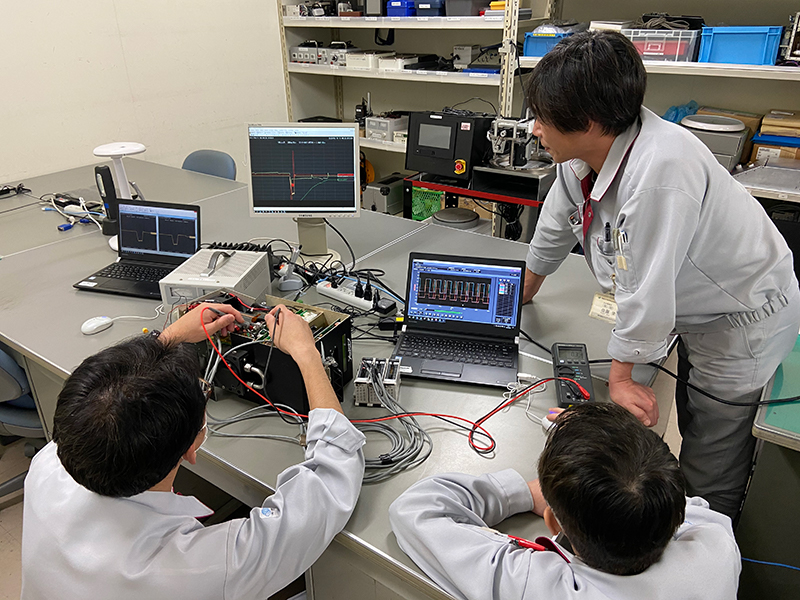
【図7 必要なものはこの部屋から生まれる。写真右の棚には、独自に作り出されたオリジナル器具が、所狭しと並んでいた】
装置が壊れたらユニットを交換する。この通常の保守・保全活動から一歩先へ踏み出して、壊れた原因を徹底的に追究することで、壊れなくする、壊れにくくするという先手を打つことが可能になる。壊れにくければ、製造設備の処理が止まることもなく、品質も納期も安定する。さらに、製造設備の耐久性を向上させることで製造コストの削減にも大きく寄与する。
常に変革への情熱を抱いて、保守・保全に携わる担当者たちの攻めの保守・保全活動こそが、長年にわたって高品質な半導体を作り続けるための秘訣なのだ。