半導体増産のカギは歩留まり向上! 不良解析時間を大幅削減したAI技術とは
2024/11/27 Toshiba Clip編集部
この記事の要点は...
- 半導体の増産が簡単にできない理由とは?
- 東芝は、AIを活用した歩留まり向上ソリューション「歩留新聞」を開発
- 自分で考える「教師なし学習」で、製造現場で手間なく使える
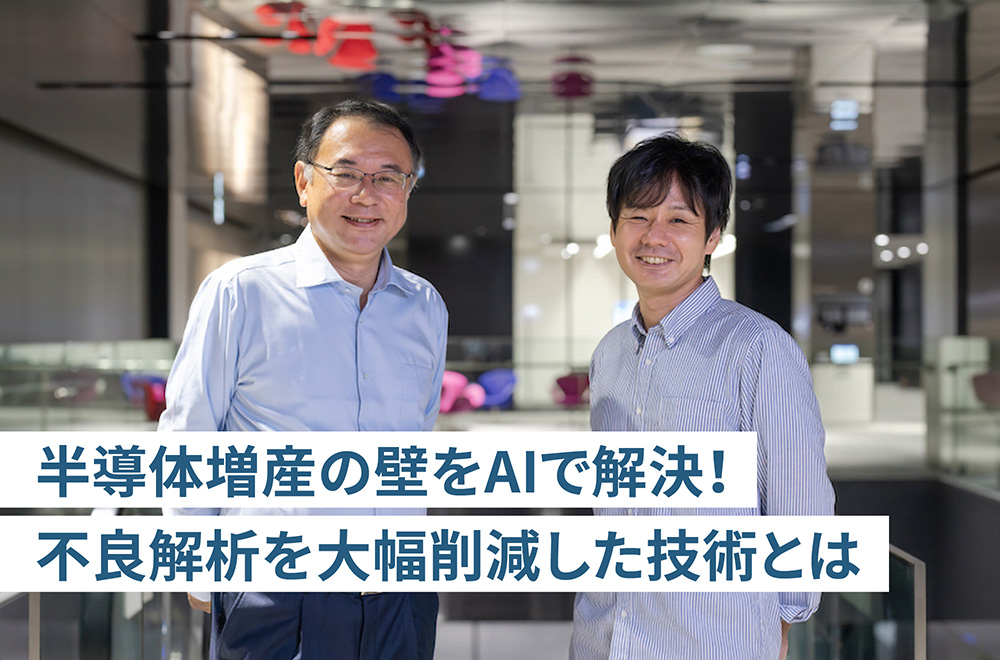
ここ数年、AI技術の進化など様々な理由から半導体需要が高まっていることはご存じだろう。もちろん半導体メーカーにとっては千載一遇のチャンスである。しかし、半導体の品薄が劇的に解消されたという話は聞かない。実は、半導体の増産は、他の産業製品に比べて非常に難しい。ましてや現在必要とされているのは、比較的高性能なAI向けの製品が中心となっているため、急速な増産体制の確立は、困難を極めるのである。
ここで東芝は、多忙を極める現場において半導体製造における不良を少ない時間で発見するAIを開発した。このソリューションを導入することで、本来1人約4.2時間/日かかっていた不良解析時間を30分に短縮するなど、約1/8に大幅削減。今では東芝の半導体工場の80%以上の製品解析に適用されており、 今後半導体工場はもちろん、他の製造現場においても適用が期待されている。長年半導体製造に携わってきた東芝だからこその技術をご紹介したい。
半導体増産のカギを握る「歩留まり向上」って?
半導体の製造には、数百から千以上もの工程が必要となる。これは、生産される半導体が高性能になればなるほど増えていくと考えていいだろう。主な工程は、ウェハと呼ばれる薄い円盤状のシリコン基板に、様々な工程を繰り返して回路パターンを形成していく。一枚のウェハが完成するまでに要する時間は、長いもので数ヶ月を要する。
完成した一枚のウェハ上には、数百から数千のチップと呼ばれる半導体が同時に作られる。しかし、一枚のウェハ上のチップもすべてが出荷できる良品というわけではない。 下の図は、ウェハの検査結果の一例である。円盤状に配置された細かい1マスがチップであり、それぞれが個別の半導体製品となる。カラフルに塗り分けられた色は、製品の良・不良の状態を表している。ざっと、赤い部分の半導体は不良品で、黄色い部分が良品を表していると考えていただきたい。
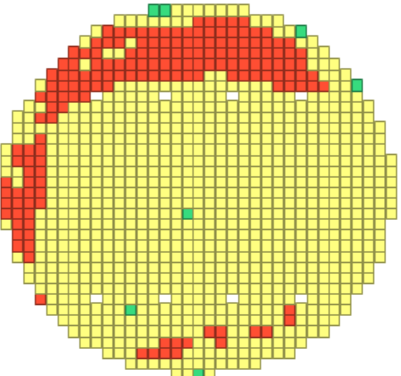
一枚のウェハ上の良品の割合を「歩留まり(ぶどまり)」と呼ぶ。歩留まり率とは、原材料に対して実際に得られた完成品の割合を指す。メーカーでは、この歩留まりが採算分岐点を超えた状態を、「歩留まりが良い」と言い、逆に赤字状態を「歩留まりが悪い」と言う。つまり歩留まり率が上がるほど採算が良くなるというわけだ。
半導体に限らず多くの製造現場では、新しい量産ラインが立ち上がってすぐに予定した歩留まりが達成されるわけではない。稼働当初は、ほとんどが不良品という極めて歩留まりの悪い状態からスタートするのが一般的なのだ。これをできるだけ早い時期に向上させて、安定した生産ラインに乗せなければならない。これが、製造技術者の腕の見せ所であり、高性能半導体の速やかな増産を阻む壁でもある。
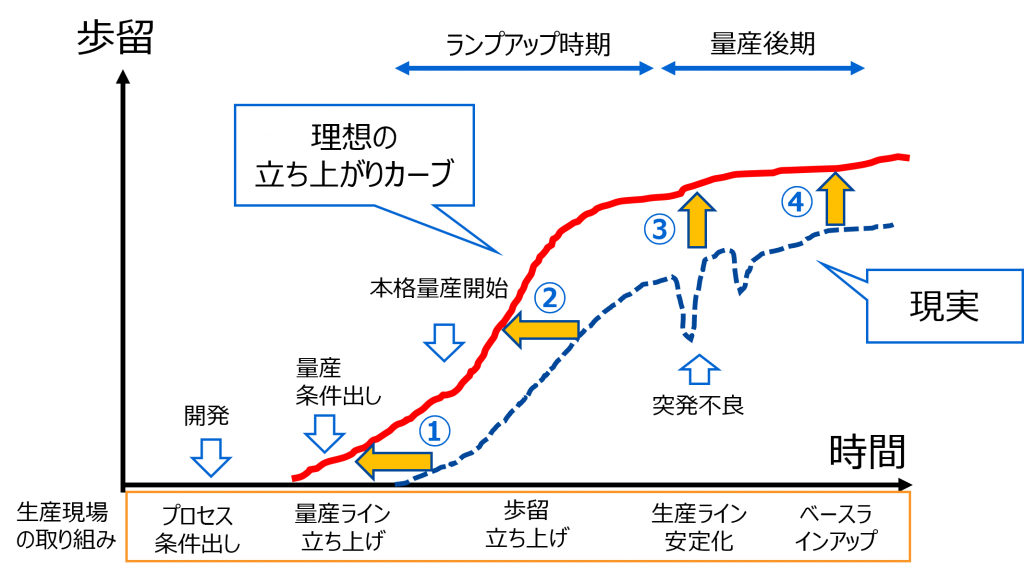
半導体の歩留まり向上はなぜ難しいのか
「現場の製造技術者は、歩留まり低下の原因を探り、改善することを日々繰り返して生産ラインの歩留まり安定を目指していきます」と語るのは、東芝デジタルソリューションズの岩佐健治氏だ。
岩佐氏は、製造現場の効率化や品質向上を目指し、製造業向けのデジタル化・自動化ソリューションを提供する、スマートマニュファクチャリング事業部の技術者である。
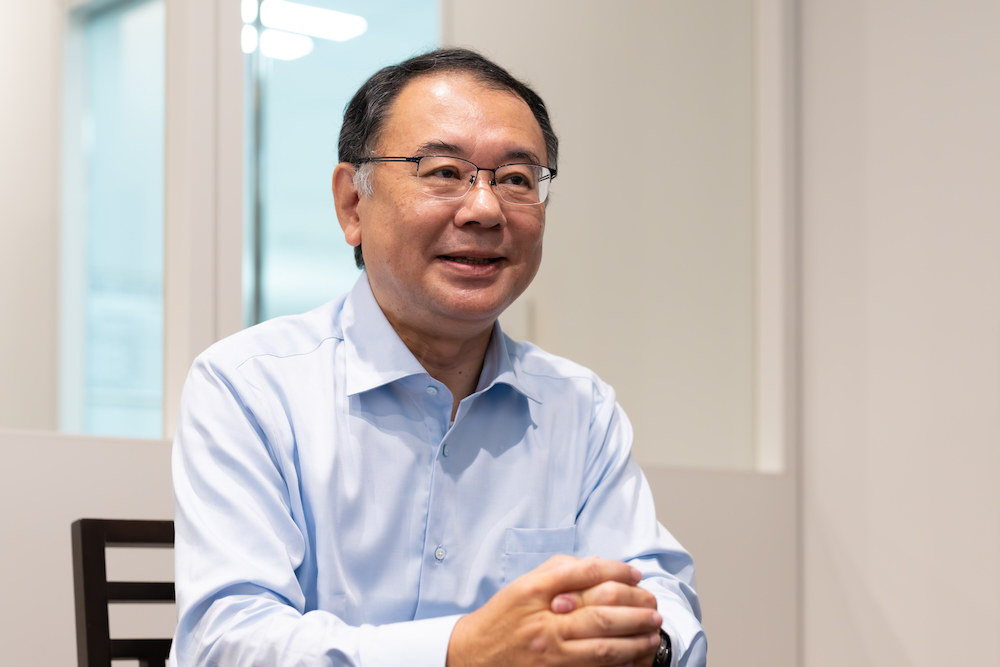
セミコンダクターソリューション技術担当 マネジャー 岩佐健治氏
岩佐氏は続けて、製造技術者の歩留まり向上への取り組みの難しさについて説明する。「製造技術者は、様々な工程の各段階で行われる検査のデータを解析し、不良の原因を特定していくのですが、数ヶ月にも及ぶ非常に長い期間、千以上もの工程で行われる検査データは膨大な量になります。しかも、それぞれのデータは異なるフォーマットで保存されているため、その整理を行うだけでも非常に大きな負担となっているのです」
熟練の製造技術者は、長年の経験によって数多の検査データの中から不良発生の原因を予想し、短期間での歩留まり向上を目指すことになる。しかし、近年の半導体はますます複雑化しており、経験と勘だけでは対応が難しいケースも増えていると岩佐氏は言う。
AIを活用した歩留り向上への東芝の挑戦
2015年、それまで製造技術者の経験に頼っていた半導体製造の歩留まり向上の取り組みに、AIを活用することを模索するプロジェクトが東芝で始まる。
「今でこそ、『AIでうまくやれるんじゃないか?』と誰もが思うような作業ですが、当時は、東芝の技術者ですらAIの能力に懐疑的な印象を持つ方が多くいました」そう当時を振り返るのは、東芝 研究開発センターでAIの研究を行う中田康太氏である。
半導体製造の歩留まり向上へのAI導入は当時珍しく、世界的にも画期的なプロジェクトであった。中田氏は、このプロジェクトに、AIスペシャリストとして参加した。
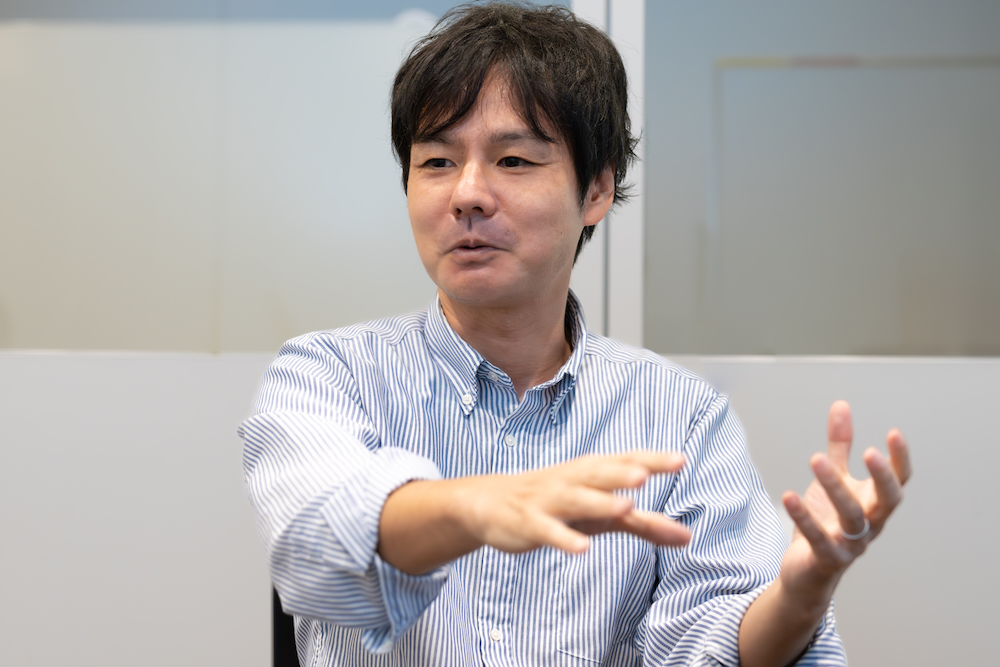
中田氏が最初に取り組んだのは、現場の技術者がどんな問題を抱えているかの調査だった。そして、歩留まり向上のために膨大な量のデータを、日々解析しているという製造現場の状況が浮き彫りとなった。
「これは、AIで強力にサポートできるんじゃないかと考えました」(中田氏)
多くの現場の助けになると、中田氏は強い思いを抱いて早速現場にこの考えを共有し、日々の解析データを提供してもらうよう依頼した。しかし、目にしたのは苦い顔をする担当者たちの顔だった。
「『AIなんて、逆に手間になるだけだろう』と、提案は予想外に一蹴されてしまったのです。良かれと思って持って行っただけに、少し辛かったですね」
技術者たちがYESと言わなかった理由は何だったのか。まず、現場で活用するAIが人の手に取って代わるには「教師データ」が必要であるという前提があった。つまり熟練の製造技術者が膨大な量のデータから何を、どう読み取っているのか、その経験を情報としてAIに学習させる必要があったのだ。
話は少し脱線するが、AI研究の歴史は意外に古く、考え方自体は19世紀にまで遡ると言われている。しかしその後、理論ばかりが先行し、実際に動作させるほどの処理能力を持つコンピュータが登場しないまま、1980年代にAI研究は冬の時代を迎える。
そして、AIが再度注目を集めることとなるのが1990年代。コンピュータの処理能力が劇的に向上し、人間の脳の働きを模倣したニューラルネットワークシステムが様々な成果を上げはじめた時だった。さらに、2000年代後半には「ディープラーニング」という言葉と共に、AIの可能性と実際の成果が次々と我々の目の前に披露されることとなる。しかし、この数十年の間、その可能性について、誰もが信じて疑わなかったものの、いつまで経っても実用化にはほど遠い、近未来の技術という認識が技術者の間でも醸成されていたのだった。
そして2020年代。AIは、熟練の技術者の判断基準など、数多くの情報を学習した上で大量のデータから最適解を導き出すことを得意とするという認識が、人々の間で浸透してきた。しかし、2015年当時、忙しい製造現場の技術者に、まだまだ実用性が実感できないAIのために自分が培った経験に基づく情報を出せとは言いづらい状況だった上に、依頼をしても断られてしまうことが多かったと中田氏は言う。
そこで中田氏は、ある方法を思いつく。
「人がAIに教えるのが難しいのであれば、AIが自ら学習すればいい」
そもそもの前提を取り除いた逆転の発想だ。こうして「教師なし学習」という手法を用いたAI利用の検討が始まった。
「まずは、『AIにできることを分かってもらうためのきっかけとなればいい』と考えました」と中田氏は言う。
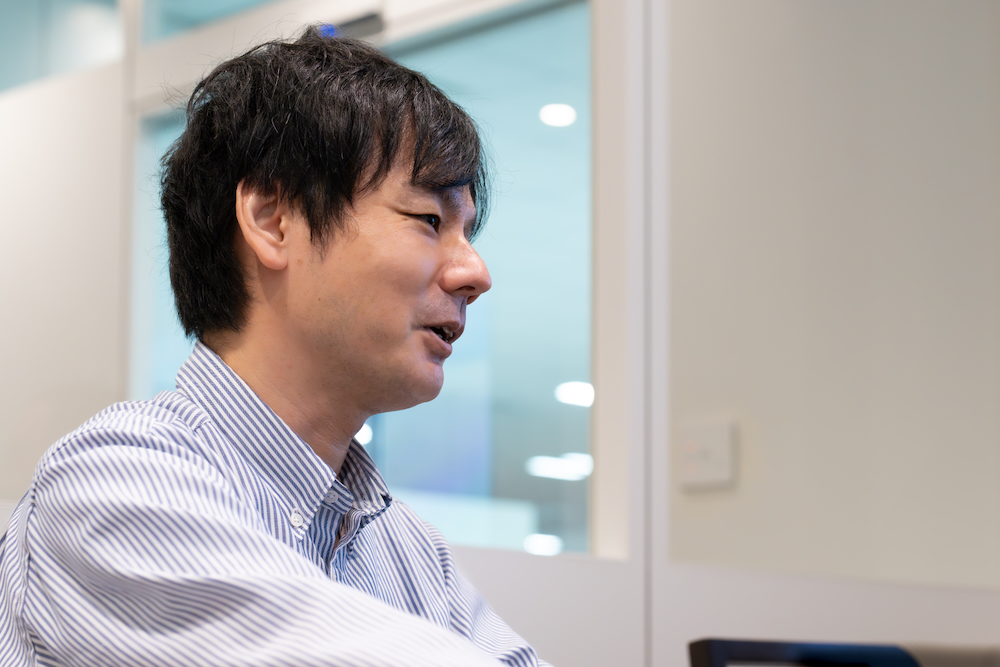
そして作り上げたのが、教師なし学習用いて、膨大なデータからウェハ上の不良パターンを自動で分類するシステムだった。AIによる自動分析には異なるフォーマットで記述された検査データを扱うことが必須であるが、前述のシステムが、見出しとなる「キー」と、値である「バリュー」によって一意に識別することのできる、キーバリューストア型のデータベースにより一元管理を行うことで、AIの活用をサポートした。こうして前日までに蓄積した大量の検査のデータを解析し、歩留り向上のための情報を朝に届けるというサービスを完成させた。
中田氏は、「毎朝勝手に届くので『歩留新聞』という名前にしました」と、少し照れながら名前の由来を教えてくれた。
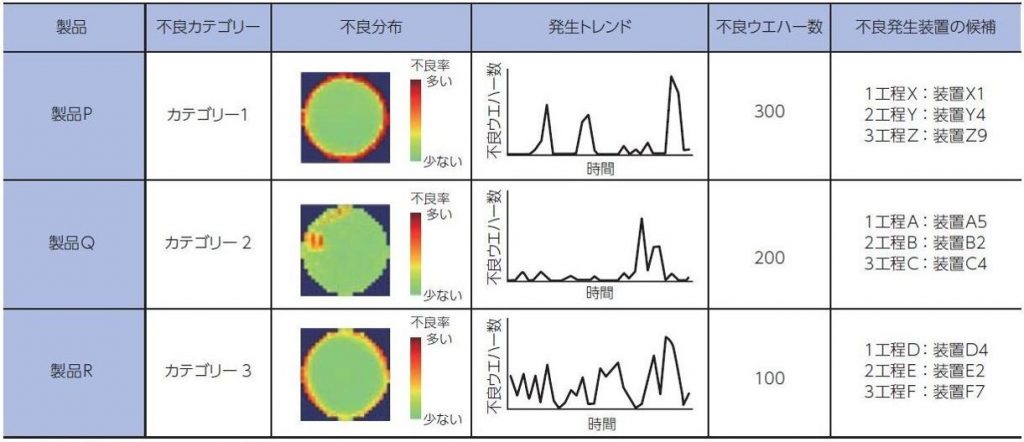
全製品、全ロットに対して網羅的な分析が可能になったうえ、これまで技術者が手作業でやっていたことをAIが実施することで、大幅に作業時間が短縮された。
さらに教師なし学習にしたことで大きなメリットが他にもあった。それは「未知の不良モード」にも対応可能になったということだ。
「工場って、生き物なんですよね。常に不良がカテゴライズできるわけではなく、新たな不良の種類が発生します。だからこそ、教師なし学習で人が気づかなかった特徴を捉え、未知の不良を可視化できる可能性があるのです」と中田氏は期待を込める。
歩留新聞の開発には、東芝が長年培ってきたデータベース技術も大きく貢献している。
「様々なフォーマットで保存されている膨大なデータを、一元管理できるデータベースを構築したことで、網羅的な分析が可能になった。AI技術とデータベース技術の融合、そして現場の協力体制。これらが三位一体となったことで、歩留新聞は誕生した」と岩佐氏は語る。
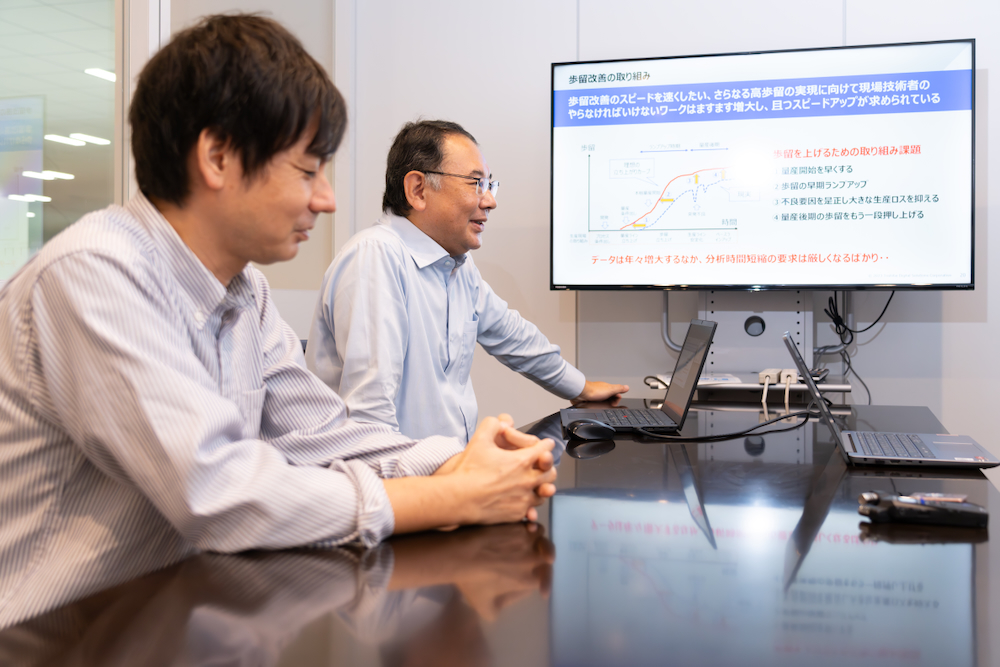
現在、歩留新聞は東芝グループの半導体工場では加賀工場、大分工場、岩手工場に展開している。今後は、ユーザーの声を反映しながら機能を拡充し、設計領域や海外への展開も視野に入れる。
「歩留新聞は、東芝のAI技術と半導体製造の知見を融合した、まさに東芝ならではのソリューションです。今後も、お客様の課題解決に貢献できるよう、進化を続けます」と岩佐氏は力強く語った。
歩留新聞は、AIが製造現場にもたらす革新の一例である。東芝は、今後もAI技術を活用し、製造現場の進化に貢献していく。