ROV Investigates Fukushima Daiichi Unit 3
2018/05/30 Toshiba Clip Team
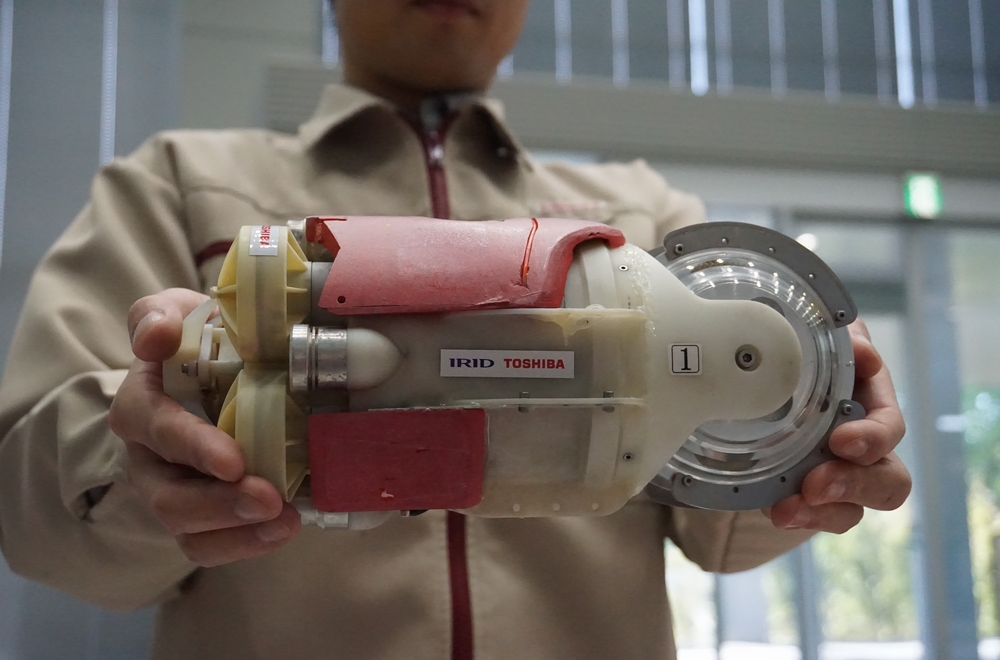
Purpose-built ROV explores interior of Unit 3 primary containment vessel
It may be a midget but this remotely operated underwater vehicle (ROV) is an intrepid explorer. Weighing in at 2 kilos, measuring 13 centimeters in diameter and 30 centimeters in length, this robot—nicknamed ”Mini Manbou” because its shape is reminiscent of an ocean sunfish—is designed to investigate the interior of the primary containment vessel (PCV) of Fukushima Daiichi Nuclear Power Station Unit 3. As a member of the International Research Institute for Nuclear Decommissioning (IRID), Toshiba developed this ROV in a project subsidized by the Japanese government. The interior of the Unit 3 PCV is flooded to a depth of 6 meters, and the ROV’s mission is to explore the bottom of the PCV as it swims around underwater.
The robot is remotely controlled via a wire cable from the remote control center about 500 meters from Unit 3. With video cameras and LED lights at front and rear, the robot illuminates its surroundings as it goes about its work. Since the access point to the Unit 3 PCV is narrow, with a diameter of 14 centimeters, Toshiba developed an extremely compact, lightweight robot that is also endowed with outstanding radiation resistance.
This video was released on December 21, 2017.
Training program reflecting lessons learned from investigation of Unit 2
Masaki Asano, who is with the Fukushima Restoration & Fuel Cycle Project Engineering Dept. of Toshiba Energy Systems & Solutions Corporation, leads the Unit 3 investigation. Recalling the investigation of the interior of Fukushima Daiichi Nuclear Power Station Unit 2 in February 2017, for which a different robot was employed, he exclaims, “It wasn’t satisfactory.” Despite plenty of operator training based on all sorts of supposedly realistic assumptions to facilitate exploration inside the PCV, the robot got stuck and came to a standstill in the middle of the investigation.
Unlike Unit 2, the Unit 3 PCV is flooded with water, which is advantageous in that a submersible robot can move around to investigate the situation in a three-dimensional space. Concerns that obstacles might prevent the robot from reaching the underground floor proved unfounded. Thanks to the robot’s compactness and the meticulous operator training in its manipulation, the robot was able to capture images of objects of interest, which are thought to be fuel debris.
“I felt relieved when we were able to capture images of what we believe is fuel debris. Inserting a pipe into an existing through hole of the PCV and then guiding the robot through the narrow pipe into the flooded vessel was particularly tricky. But my confidence in the skill of the operators who had undergone two months of intensive training proved fully justified,” says Asano.
Masaki Asano of ESS’s Fukushima Restoration & Fuel Cycle Project Engineering Dept. (left) and Kenji Matsuzaki of ESS’s Nuclear Plant Service Technology R&D Dept. (right)
Kenji Matsuzaki of Toshiba Energy Systems & Solutions Corporation’s Nuclear Plant Service Technology R&D Dept., who led the operator team, recalls: “The two months of training was certainly very demanding, with a tight schedule. Naturally, we wanted to simulate the actual site, but it was impossible because the conditions inside the damaged structure were completely unknown. So we placed all sorts of obstacles and created a lattice structure through which the robot could just about pass. In the course of repeated training, we honed our skills to the point that we felt we were capable of dealing with just about any situation.
“Thanks to the tough training using the mockup, the objective of the investigation was achieved 200%! I am no longer troubled by a recurring nightmare in which the robot gets stuck and stops moving through the water,” says Matsuzaki. The success of the investigation of Unit 3 is in large measure attributable to the dedication and perseverance of the operators throughout their training.
Making the robot smaller while increasing thrust
The greatest challenge in developing the ROV was to increase thrust while making the robot smaller. Since the robot is connected to a cable that is prone to entanglement as the robot moves around inside the PCV, the robot had to be equipped with a compact yet high-power motor so that it wouldn’t get stuck. To accomplish this, the control circuit became very complicated and it was difficult to incorporate it in the ROV. A cable with minimal friction was developed. During their training, the operators mastered the technique of guiding the robot forward and backward while keeping the cable taut to prevent entanglement with adjacent structures.
An ROV can also be used for periodic inspection of structures inside the reactors of plants that are in operation. Although wired control is a limiting factor, this robot can move around flexibly in a three-dimensional space, and so the robot may be suitable for general-purpose applications.
For retrieval of fuel debris
Based on the results gained through the investigation of the PCV by the ROV, Asano and Matsuzaki are eager to proceed to the next step, including investigation of the conditions inside the reactor pressure vessel and retrieval of fuel debris. Reflecting their resolve to help deal with the challenges posed by the circumstances at Fukushima Daiichi Nuclear Power Station, they are eager to continue contributing to the vital work at the site. Matsuzaki says, “Robots really come into their own in the environment at Fukushima Daiichi. For robotics engineers, it is highly motivating that the robot we develop will swiftly be applied for practical purposes.”
Summing up the investigation of the Unit 3 PCV Asano stresses, “The achievement of our initial objective at Unit 3 has given us confidence. Our concerted efforts—covering thorough training in operator skills, assumption of risks, and implementation of countermeasures—is bearing fruit.”
From now on, their focus will shift to R&D of equipment for fuel debris retrieval with a view to the decommissioning of Fukushima Daiichi Nuclear Power Station.