The Science Behind Nanofiber Electrospinning Technology
2019/03/27 Toshiba Clip Team
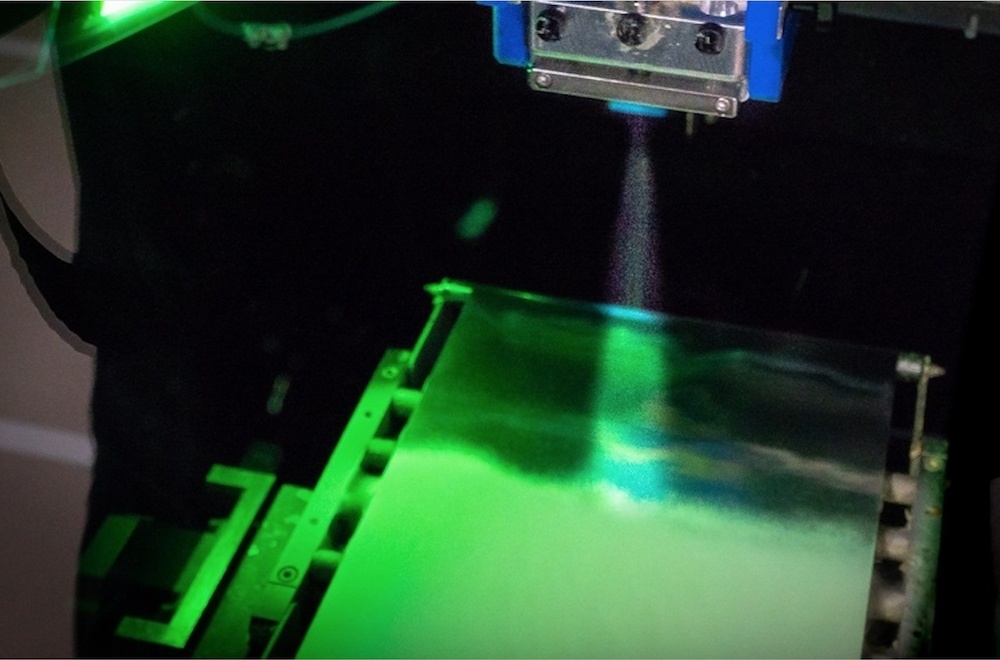
Nanofiber electrospinning is one of the complex technologies today and is expected to be applied to Toshiba’s SCiB™ lithium-ion rechargeable battery. How are ultrafine fibers created? Ikuo Uematsu, responsible for the development of electrospinning technology, shares the basics of nanofibers, electrospinning technology used to fabricate them and its appealing features.
Ikuo Uematsu, Process Technology Research Department, Corporate Manufacturing Engineering Center, Research & Development Division, Toshiba Corporation
What is electrospinning technology?
Nanofiber membranes consist of ultrafine fibers with thicknesses typically ranging between 1 nm and 100 nm, and lengths of around 100 times their thickness. There are many types of fibrous materials, such as nylon and cellulose. The ultrafine property of nanofibers supports our daily lifestyles in various ways.
Nanofibers
“One easy-to-understand example of the use of nanofibers is in the filters used in appliances such as air purifiers and water treatment facilities. Nano-sized fibers are ideal for use in filters because they are not very susceptible to air or water resistance,” explains Uematsu.
“Another application is rechargeable batteries. The starting point for me getting to grips with nanofibers initially was when I became involved in the launch of Toshiba’s SCiB™ rechargeable battery project. We wondered if maybe we could use nanofibers in SCiB™ rechargeable batteries which requires a material called a separator (*). If we replace this separator with an ultrathin nanofiber membrane, then we can increase the capacity of the battery.”
*The separator is an insulating material placed between the electrodes of a battery to prevent short circuits.
The principles behind this technology
“First, we dissolve the material which we want to make into nanofiber into a solution, and insert it into a needle-shaped nozzle. We then apply a high-voltage electric current to the nozzle. When we do so, it creates a difference in electrical potential between the solution inside the nozzle and the base material to which we want to apply it. This gives rise to forces between the nozzle and the base material, and the solution is drawn out of the nozzle towards the base material. Since the solvent (*) evaporates, the weight of the solution/material decreases, and the stream of material gradually flares outwards towards the bottom. In this way, nanofibers are formed on the surface of the base material,” Uematsu explains.
*A solvent is a liquid used when dissolving a material to create a solution.
The solution is drawn out of the nozzle as the high-voltage electric current is applied to it, forming nanofibers on the base material.
The conventional mainstream approach in the development of electrospinning technology has been to aim to produce finer, more uniform nanofiber membranes. However, pursuing these characteristics further than necessary leads to steep increases in production costs, and while there had been many development projects involving electrospinning technology at the research level, there were only a few examples of its application in mass production. In view of this, Uematsu decided to change his way of thinking.
“In working towards the application of (electrospinning) to SCiB™, I thought that we needed to acquire a high-speed nanofiber formation technology that was specialized towards mass production without seeking to achieve excessive fineness and uniformity. This was a new area of research for us.” says Uematsu.
Understanding the Complex Behavior of this Seemingly Simple Technology
Image of the nanofiber fabrication
With electrospinning technology, nanofibers can be formed simply by setting the material and applying a voltage to the nozzle. In this sense, it is a very simple technology. What is more, the distance between the nozzle and the base material to which it is being applied is only between 20–30 cm. This small gap influences the behavior of the system—in terms of how the solution travels over that distance and how the material changes from liquid solution into solid nanofiber—is complex and requires precision and careful handling.
“In order to apply electrospinning during the manufacturing of the products, it is necessary to form nanofibers at high speed using multiple nozzles. If the number of nozzles is increased, the voltages applied across each nozzle will interfere with one another, and it becomes difficult to form uniform nanofibers. Our aim was to achieve consistent mass production of nanofibers by unravelling the secrets of this “20 cm behavior,” explains Uematsu.
Uematsu discusses the challenges that he and his colleagues experienced during the development process.
Naturally, he says that there were challenges during the initial development stages.
“At the initial stages, the fibers that we created were weak, and far from anything that could be used in practical applications. We pooled knowledge and experience from various development teams and one idea—which came from experiences in the development of inkjet printers(*)—was to film, analyze and quantify the stream of fiber coming out of the electrospinning nozzle using a high-speed camera, in order to try and understand its behavior over the distance of 20 cm. This was one of the memorable breakthroughs,” reflects Uematsu.
*In the development of inkjet printers, high-speed cameras are used to film, analyze and quantify how droplets of ink behave as they fly out of the inkjet nozzle.
Behavior over 20 cm
The behavior of the nanofiber stream over a distance of 20 cm changes in various ways depending on factors such as the size of the voltage applied, minute differences in distance between the nozzle and the base material, and types of nanofiber material and base material. One aspect of behavior that caught the team’s attention was the angle at which the stream flies out of the nozzle. The angle of the spiral formed by the solution during flight with respect to the material to which the nanofiber is being applied becomes gradually smaller as it approaches the base material. The team quantified this angle.
Another aspect of behavior that the team focused on was the speed of flight. Through filming and analysis using a high-speed camera, the team was able to understand the relationship between angle and speed of flight, which proved to be a real breakthrough in terms of achieving mass production.
The team made a huge leap towards mass production by filming and analyzing angle and speed of flight.
“In 2018, we finally succeeded in creating a prototype applying electrospinning technology in the production of SCiB™. The idea for this development was first conceived in 2012, so it has taken us six years to reach this point. Four years have passed since we began full-scale development efforts. What really added to the joy I felt when we succeeded in creating the prototype was the thought that we had continued in our development efforts together, based on the sentiment that our colleagues in the SCiB™ project and many other people around the world needed this technology,” says Uematsu.
In the past, applying electrospinning to product manufacturing was considered difficult. The development efforts of Uematsu and his team will undoubtedly change the world in an enormous way, through the creation of extremely fine nano-sized fibers utilizing this technology.
Related Links
*This section contains links to websites operated by companies and organizations other than Toshiba Corporation.
https://www.reuters.com/brandfeatures/road-to-a-new-day/powering-smart-cities-with-lithium-ion-batteries?utm_source=referral&utm_medium=toshibaclip&utm_campaign=prtoshibaclip&utm_term