A Blue Ocean Strategy Protects Infrastructure -Securing the world’s bridges with the power of digital technology
2023/12/06 Toshiba Clip Team
- Preventive maintenance with X-ray like inspection.
- Sensing technology that can save trillions of yen.
- “Impossible,” they said, but a blue ocean lay ahead.
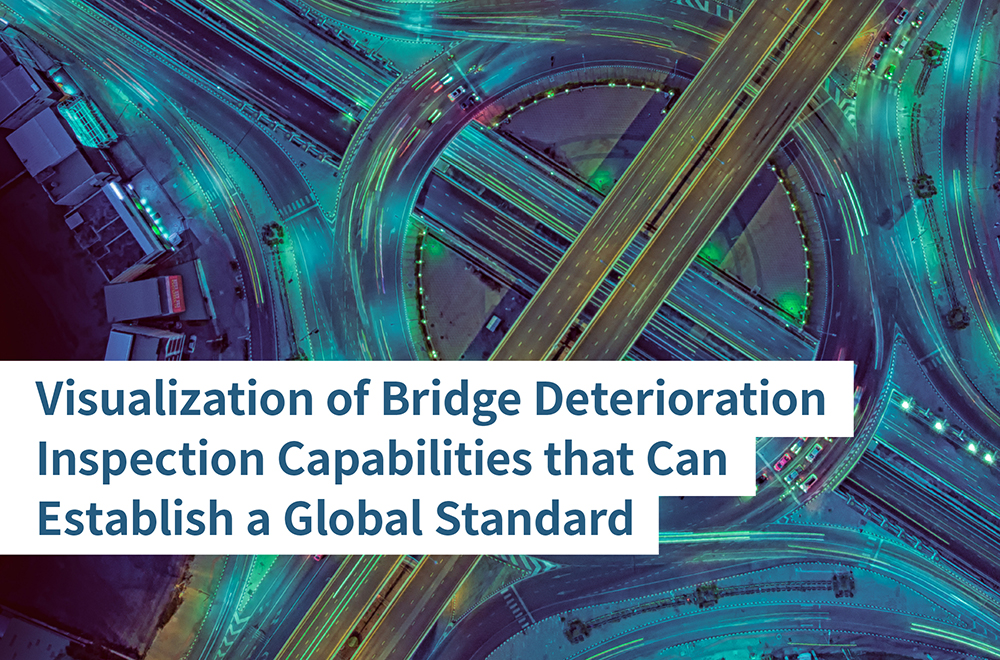
In October 2021, the Biden administration signed a $1 trillion infrastructure investment bill that put a strong emphasis on rebuilding roads and bridges. Aging infrastructure is something Japan also has to face. Highways built during the years of high economic growth show serious signs of deterioration, and in 2012 there was a tragic accident when concrete ceiling panels in an expressway tunnel collapsed onto passing cars, killing some people and injuring more. Watabe, a researcher at Toshiba’s Research and Development Center, is keenly aware of this problem, and believes “Toshiba should take measures to deal with aging infrastructure.” We talked to him about it.
About 700,000 bridges in Japan need to be inspected and maintained to ensure their integrity
For a long time, concrete structures were thought of as permanent, something that would endure for over 100 years,” says Watabe. “The reality is that the rebar used to reinforce concrete rusts and expands, causing cracks. Bridges are also damaged because vehicles carry loads that are much heavier than anything expected when the roads were constructed. We now know that proper repair and reinforcement is essential for a bridge to last 100 years, and even the Ministry of Land, Infrastructure, Transport and Tourism has set 50 years as a guideline for age-related bridge deterioration.”
Kazuo Watabe, Fellow, Mechanical Systems Laboratory, Advanced Intelligent Systems Laboratories, Corporate Research & Development Center, Toshiba Corporation
The potential scale of the problem is immense, as Watabe explains. “Japan has more than 700,000 bridges over two meters long. Only about 500,000 have a documented construction date, and of those 39%, approximately 200,000, will be over 50 years old by 2023. Adequate inspection and maintenance to ensure their integrity is essential.” However, as he goes on to reveal, there is another dimension to the problem: a dwindling number of skilled technicians. “Currently, bridges are, basically, visually inspected. People check them individually, one by one. But the construction industry has an aging workforce, and we cannot rely on skilled workers to inspect bridges and other civil engineering structures forever.”
Maintenance reliant on skilled workers is increasingly difficult
In responding to these social issues, many companies are looking to use drones and AI to inspect surface images of bridges. Toshiba, which has built a wide range of infrastructure, is also taking advantage of its cumulative know-how and proprietary technologies to take on the problem—however, its approach is different.
Realizing preventive maintenance with a visualization technology like X-ray inspection
The impetus for Toshiba’s initiative came from participation in “Robot and Sensor System Development Project for Infrastructure Maintenance and Disaster Surveys,” a national project that ran from fiscal year 2014 to 2018, sponsored by Japan’s New Energy and Industrial Technology Development Organization (NEDO).
One participant in the Toshiba effort was Hidefumi Takamine, who also works at the Research & Development Center. “Toshiba’s strengths lie in the manufacture of sensors and signal processing terminals, system construction, and AI analysis,” Takamine says. “We started by thinking of how we could contribute in those areas.”
Hidefumi Takamine, Specialist, Mechanical Systems Laboratory, Advanced Intelligent Systems Laboratories, Corporate Research & Development Center, Toshiba Corporation
Another participant in the initiative was Tomoki Shiotani, a Program-Specific Professor at Kyoto University, who collaborated with Toshiba on joint development of non-destructive sensing technology for assessing internal deterioration in concrete structures. Toshiba has now started using the technology to visualize the internal status of bridges and to analyze their soundness.
“You can think of our technology as like bringing radiography into medicine, which had long relied on sight, sound and touch during examinations,” says Watabe. “X-rays made it possible to see problems before symptoms appeared, and to prioritize treatment.”
As Watabe explains it, the technology does the same, visualizing the interior of concrete and allowing inspection for cracking and deterioration. “There are many cases where the problem is not visible from the outside, but the inside has started to degrade. Technology for that kind of inspection has rarely been used in the field,”
He goes on to explains that the basis of today’s approach to maintenance management is reactive maintenance: visual damage is detected, and measures are taken only after a structure fails. However, the Ministry of Land, Infrastructure, Transport and Tourism wants to get away from this approach, and is promoting preventive maintenance that can inspect for deterioration at an early stage and initiate action before problems get serious.
Differences between preventive maintenance and reactive maintenance
A sensing technology that could help save 90 trillion yen
Estimates by the Ministry of Land, Infrastructure, Transport and Tourism indicate that reactive maintenance over the 30-year period from fiscal year 2018 to fiscal year 2048 will cost as much as 284 trillion yen, but that the cost of preventive maintenance comes in at 194 trillion yen—a saving of approximately 90 trillion yen. The technology developed by Toshiba and Kyoto University can contribute to this preventive maintenance, as Watabe explains.
“The core of the technology is acoustic emission sensors that are placed on the underside of the concrete decks installed on bridges. These AE sensors detect vibrations that propagate as elastic waves when vehicles cross the bridge; waves that can be used to detect deterioration or damage in the concrete. If there are no cracks or deterioration, the elastic waves should be close to what we expect theoretically, but if there’s a disturbed waveform, we can identify deterioration.” Watabe says that there are other advantages, too: there is no need for traffic control during inspection, and inspection times are shorter and cost less.
Overview of the AE sensor technology that contribute for realizing preventive maintenance
“Impossible,” they said, but a blue ocean lay ahead
Watabe continues, “It was pure luck that I came up with the idea of using AE sensors for bridge inspections. Few other companies were taking this approach, because of the problem with noise—but at the end of it all we found a blue ocean.”
Asked exactly what the problem was, Watabe is happy to explain: “While it’s theoretically possible to find internal damage or deterioration in waves detected by AE sensors, those waves are too weak to use to detect anomalies in bridges that have a lot of traffic, because the noise drowns the signals, Even Toshiba engineers who use AE sensors to inspect other infrastructure equipment were skeptical of this approach.”
In fact, Watabe had good reason to be wary about taking on the idea. Just before starting to participate in the NEDO national project, he and Takamine had the bitter experience of being involved in a business that was stopped.
“Back then, because of the withdrawal, I was a bit of a ronin, without a fixed base in the company, ” says Watabe. “I got involved in this project with a sense that it was a career change. I am basically a competitive person, and I told myself that this was not the time or place to be discouraged, that being involved in the NEDO project to find ways to inspect infrastructure integrity was an opportunity and challenge.” This was also the time when Takamine came up with an idea for solving the noise problem when using AE sensors to inspect bridges.
“It’s true that when we installed AE sensors on a bridge, the waves were lost in the noise,” “But then I had this thought… Why not turn things around and use the noise? So what we did was to use noise to increase the data, and from that we extracted only the signals related to soundness. We then analyzed the signals to pinpoint the locations of damage or deterioration. We also made sure that the more data we accumulated, the more accurate the analysis became. This method was only possible because of Toshiba’s filtering, analysis, and mechanical core technology for understanding physical phenomena.”
Takamine was not originally an AE sensor expert. According to him, “I looked at this with the fresh eyes of an amateur, and I envisioned the phenomena that I thought should be there, as a reverse way of thinking.” One thing beyond doubt is that this approach led to many proprietary technologies, and carried the project team toward a dream goal for all researchers, a blue ocean: the discovery of a new market where there are no competitors, and where the pioneers can define the way forward.
Now, Toshiba, in cooperation with the technology’s co-developer, Professor Shiotani, is promoting industry standardization. The Japanese Society for Non-Destructive Inspection has already established a new standard, NDIS2434, and similar moves are underway overseas.
Strategic differences between Blue Ocean and Red Ocean
Watabe is very much aware that these are still early days for the technology. “Using AE sensors for bridge inspections is new and does not yet have a long track record,” he notes. “However, having a technology standard like NDIS2434 makes it easier for people to use the technology.”
Watabe looks further into the future. Into the world.
And Watabe is not just looking at making it easier in Japan. “Concrete decks are used in bridges all over the world, so if we can get a record of results in Japan, we can expand overseas,” he says. “Professor Shiotani and a technical committee of experts from European organizations are working on a draft proposal for standardization. If this technology does become standard, companies will be able to efficiently implement measures to deal with their country’s aging infrastructure; after all, Toshiba alone cannot diagnose all bridges. However, there are many business opportunities to be found in resolving social issues, and I think that for Toshiba, whose corporate philosophy is to contribute to society, this is the kind of work we should do.”
Fukuoka Urban Expressway Demonstration Tests Confirm Project Results
Entering 2020, the technology for nondestructive sensing of internal deterioration in concrete structures took a big step forward with two demonstration tests on the Fukuoka Expressway, in the north of Kyushu, the most westerly of Japan’s main islands.
By that time the expressway, which opened to traffic in 1980, had been in operation for over 40 years, and the main concern was preventive maintenance. The Toshiba team focused on visualizing and analyzing the soundness of decks on a bridge on Fukuoka Expressway Route 1, with traffic running.
“With our first demonstration experiment we aimed to “confirm validity,” recalls Watabe. “Eighteen AE sensors were installed on a four by one meter concrete deck, and effective data filtered from the waves generated by vehicles crossing the deck was analyzed with a number of signal processing techniques. This analysis generated a soundness map that showed healthy areas in blue and damaged or deteriorated locations in red.”
Soundness map based on signal analysis and actual damage matches
A small hole, shown in light red on the soundness map, was bored in a location determined to have “slightly damage,” and inspection with an endoscope found a crack of about 0.2 mm. Blue areas diagnosed as sound were found to have no abnormalities.
Commenting on the results Takamine said, “This has demonstrated a good degree of validity,” and Watabe was also optimistic: “We are now in a position where we can apply this system to bridges and carry out inspections on a one-day basis We can now see the way forward to developing the business as an all-in-one service, from inspection to analysis.”
The second demonstration experiment was about using the technology to visualize the results of concrete repair. The ability to confirm that repairs to concrete are done properly makes it possible to prevent oversights in current repairs and reduce future repair costs.
“The usual method for repairing cracks is to fill them with resin,” explains Watabe. “This is done by using an injector to push the resin into the crack and letting it harden. However, deciding whether or not the crack is completely filled is often based on the volume of injected resin, which leaves room for doubt. We used our technology to get more accurate confirmation.”
The bridge was inspected prior to repair, producing a soundness map that was dark red over almost its entire surface. Once the bridge was repaired, the map was blue, indicating successful repair of the bridge. “This result shows that the technology can be used to assess repair work,” says Takamine. “It really expanded the scope of use.”
Visualization of deck repair
A sense of mission: “Toshiba is the one to do it.”
That expansion extends to potentially using the technology in other areas. “We are still in the process of verifying the technology,” says Takamine, “but in principle it can be used for other concrete structures. We are putting all our energy into the current development work, but we are also thinking about it in parallel.”
The project faced adversity from the very start, to the point where experts on AE sensors said it was “impossible.” Watabe reacts to that now with a laugh. “We are tackling it as a completely new business.” Of course, doing that is no easy challenge, so what reason is there for not giving up and for continuing? Both Watabe and Takamine have an emphatic answer: “It is something that a company like Toshiba should do.” Watabe tells a story that throw more light on that.
“During the course of the demonstration experiments, we came to realize the power of the Toshiba brand. When we asked related parties to cooperate, we were never turned away at the door, not once. Even with new initiatives, they listened to us. But that was nothing to do with my capabilities. Toshiba has a lot of world-first technologies, and also provides products and services for essential infrastructure like power plants. Toshiba has always been a company that solves problems the world faces. A decades-long history of such efforts has earned Toshiba trust. If people trust us, we must respond.
“We will use our technologies to help address aging infrastructure and win further trust by solving social issues. I believe that Toshiba, with its philosophy of ‘Committed to People, Committed to the Future.’ should be doing this kind of work.”
Contact us | Inquiries to Corporate Research & Development Center | Toshiba (global.toshiba)