Inspection Robots Get the Job Done in Half the Time! -Helping to ensure a stable energy supply globally!
2024/02/05 Toshiba Clip Team
- Toshiba robots cut turbine generator inspection times in half!
- What is the approach that the engineers take, who develop cutting-edge technology and incorporate it into society?
- Simplicity brings trust when it comes to devices. The pride of engineers who support social infrastructure.
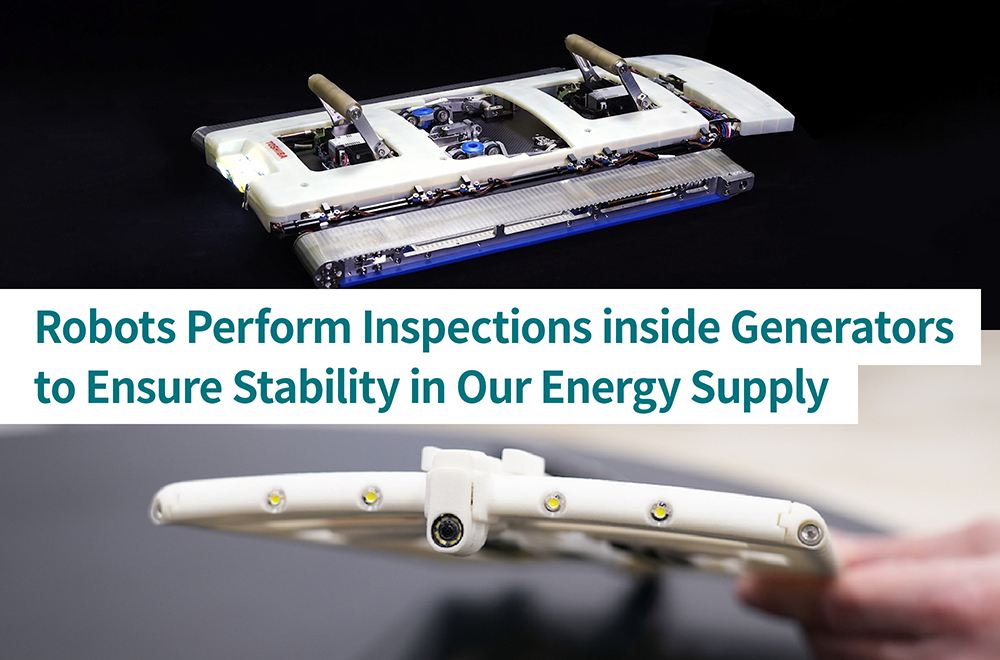
“Supply and demand for electricity is balanced on a knife edge around the world, and everyone knows this is a major problem,” says Dai Nozaki of Toshiba Energy Systems. The stability of the energy supply that underpins our daily lives depends on complex factors, including geopolitics and the drive toward carbon neutrality. Stability of energy supply is a pressing issue in every country, and so streamlining regular inspections of the power generation facilities that play a major role is a high-priority issue for utility companies. When it comes to drastically reducing the time required for these inspections, the solution is inspection robots.
Nozaki oversees the development and rollout of ultra-thin and multi-functional versions of these robots. While Toshiba is a latecomer to the U.S.-led inspection robot market, Nozaki is confident that Toshiba can prevail. We asked three main players behind the scenes in the development of robots with the potential to play a fundamental role at power plants around the world, how Toshiba intends to commercialize its strengths and seize its opportunity in this market where competitors are jostling for prime position.
Dai Nozaki, Specialist, Electrical Systems Design Group 1, Nuclear Electrical Systems Design Division,
Isogo Nuclear Engineering Center, Toshiba Energy Systems & Solutions Corporation
The use of robots drastically reduces the time needed for generator health checks!
Thermal and nuclear power plants use steam to turn turbines, and convert the energy from this rotation into electrical energy. How does an inspection robot work in this mechanism? Nozaki, who leads the inspection robot project, offers the following explanation.
“During a precision inspection every four years, a rotor (the revolving part) weighing several hundred tons is pulled out of a turbine generator for many days, and then specialized inspectors manually check the rotor and stator (the stationary part). However, inspection robots can get into the small gap between the rotor and stator, enabling automatic inspections to be completed in around 12 days – about half of a normal inspection.
With a simple inspection that does not require the rotor to be removed, the robot obtains data that can be used to understand state of the equipment. This data can then be used to plan efficient maintenance. Going forward, we want to shift regular inspections from time intervals to the state of the equipment,” says Nozaki.
Turbine generator cross section
What are the advantages of the multi-functional inspection robot?
Toshiba has unveiled two types of inspection robots, so let’s first take a look at the multi-functional version first. Yoshinori Kurita of Toshiba Electronic Technologies Corporation explains this here. Kurita has worked on projects such as ATMs (automated teller machines) and passport issuance machines, and joined the multi-functional robot project based on these skills.
Toshiba’s multi-functional inspection robot with its arms extended from the top.
“The multi-functional type was unveiled in 2018. Until then, it was necessary for a person to pull out the rotor, and to perform a hammer test on the stator for wedge loosening check, and to conduct a visual inspection for clogging ventilation holes int the rotor by using a fiber scope. But now, since a robot performs these, the inspection time can be reduced, and the accuracy can be improved.
In order to verify that the robot was working as intended, we needed to test it on a real power plant. It would usually be quite much difficult to test an in-development product on an actual working generator, but in this project, we were able to do just that thanks to the cooperation from our partner power company, and this was possible because of the trusting relationship.
At Toshiba, we worked with acoustics expert and robot control expert. After emphasizing the high functionality of this robot, lots of the testing was done to verify its reliability and whether user-friendliness was sufficiently incorporated into the design. That really motivated me,” says Kurita.
Yoshinori Kurita, Manager, Machine Designer,
Social Systems Technology Department, Systems Division, Toshiba Electronic Technologies Corporation
Some turbine generators have partitions called baffles to improve internal cooling performance in the gap between the rotor and stator where the robot travels. These obstacles prevented the robot from moving. The robot was equipped with arms extending from the top, allowing it to overcome the baffles before it retracted the arms and moved on. This ability to deal with baffles differentiates Toshiba from competitors.
But the challenges did not end there; the COVID-19 pandemic hit. While it would normally be possible to assemble this robot in a month or two, suppliers were stuck and Toshiba was unable to obtain parts such as connectors as expected. Kurita recalls how he and his colleagues dealt with the situation by modifying existing products.
“At Toshiba, we believe in technology. When we are faced with a challenge, we use technology to overcome it and reach the required level. This reflects the “Look for a better way” approach we take. We know that we can trust our experts to get the job done, and that as long as we fulfill our role, the project will move forward as a whole. This is the kind of reassurance.
Of course, age is not an issue; one of the members in this project had been at Toshiba for less than a year after graduating university. Having actual contact with things they designed is a valuable opportunity for engineers, and leads to tremendous growth. At Toshiba, we actually get to see the thing we designed,” says Kurita.
Group photograph during an inspection at a nuclear power plant overseas
– Create together – the approach that underpins the development of cutting-edge technology
Although it’s not widely known, the development of inspection robots is led by several companies, mainly from the US. Toshiba began development in 2015, and to transform itself from a latecomer to a leader, it is taking on the challenge with high functionality and ultra-thin design as described above.
The source of this strength to continuously achieve world firsts is the company’s value of “Create together”. This means combining expertise, working together towards a common goal, growing together and creating a new future.
When the idea of multi-functionality and ultra-thin design was put forward, experts in the areas of generators, acoustics, machinery, controls, and others proactively expressed interest in undertaking the development and came forward to form a team. This seems to be a common occurrence at Toshiba.
“Toshiba has a culture of designers and manufacturers working together in development. I was so impressed by the cooperation for the “Create Together.” The manufacturers understood the design that had gone through a lot of effort and made it a reality very carefully. This is the way engineers work at Toshiba”. Said Mitsunori Yuminamochi of Toshiba Electronic Technologies Corporation, who led the development project for the ultra-thinrobot.
Mitsunori Yuminamochi, Expert, Machine Design,
Social Systems Technology Department, Systems Division, Toshiba Electronic Technologies Corporation
“The impact of Toshiba’s value of “Create together” also extends beyond the company itself. The fact that they had got the cooperation from a power company during the development phase accelerated its success. With the support of any players, they were able to take the project to unprecedented heights.
“For the ultra-thin robot, we succeeded in developing one of the thinnest products in the industry. We got the thickness down to 10mm, which is drastically thinner than the 33mm of the multi-functional version.
The gap between the rotor and stator in a turbine generator is around 10 to 60mm. This gap is narrower in medium and small generators than in large ones. Toshiba’s inspection robot has made it possible to inspect in tight spaces,” says Yuminamochi.
The robot is packed with Yuminamochi’s ingenuity, such as a slim-line design that leverages the characteristic of 3D printers to enable integration of all necessary functions into one place, and the selection of a structure suitable for slim-line design based on his previous experience in mechanical design.
Toshiba’s ultra-thin inspection robot
The most trusted devices are the simplest ones.
How did they overcome the challenge of creating a thin, light, and highly reliable robot in a short time? Yuminamochi had actually been involved in the design of radars, space satellites, and other such things that require precision, which makes him an expert in machine design.
“With satellites, it’s not possible to resolve any problems that occur after launch into space. So before launching, we have to go through a process of repeated testing and verification, and create a product that offers absolute reliability.
In the case of this robot, if a part of the robot falls off or breaks down inside the generator, the only way to get it out of the tight space is to disassemble the generator. Extremely high quality was needed, and that fact brought a certain tension to the project,” says Yuminamochi.
When asked what is the most important in developing highly reliable devices, Yuminamochi gives a somewhat unexpected answer.
“Keep it simple.”
The more complex a machine is, the more difficult it is to improve its reliability in a short period of time. The skill of engineers is reflected in the extent to which they create simple mechanisms when incorporating customer requirements into the performance.
“Keep it simple. My experience in designing machines was reflected in the development of these inspection robots. The problems and solutions we encountered in developing the multi-functional version were used in developing the ultra-thin version. However, we still had some difficulties in reducing the size,” says Yuminamochi.
Although it is thin and small, it still requires the power to pull a cable. Achieving a balance between them required a lot of thought. In addition, many of the leading technologies for inspection robots are the subject of patent applications overseas.
“It was pretty tough to undertake development without infringing on any patents. But in the end, we successfully developed a slim-line, lightweight, high-performance robot by learning and surpassing the technologies of our competitors,” says Yuminamochi.
The multi-functional robot pushes its three arms against the surface of the stator when it travels, and is capable of handling every aspect of inspections. The ultra-thin robot adheres to the stator’s surface using magnets, and is capable of handling every aspect of inspection except the ultrasonic tests of rotors. Combining the two leads to the finest results.
The multi-functional robot and slim-line robot both have their own specialties
Proud to support social infrastructure, they work on the next production
Toshiba inspection robots are used in thermal and nuclear power plants around the world, contributing to the stability of energy supplies. Toshiba’s commitment to solving social issues is based on its philosophy of “Committed to People and Committed to the Future.”
As the leader, Nozaki focuses on the next target and says, “What we need to do first is to build up our track record in robot inspections.” Inspecting turbine generators with robots will lead to the identification of new challenges and demands from power companies. They will be shared with engineers and used to develop robots to meet customer needs better. Always aiming high is the DNA of Toshiba engineers.
Finally, we asked the three people we talked to about their vision.
“I am in the Electrical Systems Design Department for nuclear power. I would like to go beyond turbine generators, and realize robot-based and online inspections of electrical systems in power plants,” says Nozaki enthusiastically.
“I joined Toshiba with a desire to work in manufacturing, and I am still proud of being able to contribute to society through mechanical design and engineering. I really hope to keep this up,” declares Kurita.
“As an engineer, I will keep making lots of products that exceed people’s expectations. In addition, I hope to work with young people, help them feel the fun of work, and take responsibility for the development of the next generation,” says Yuminamochi, paying attention to skills training.