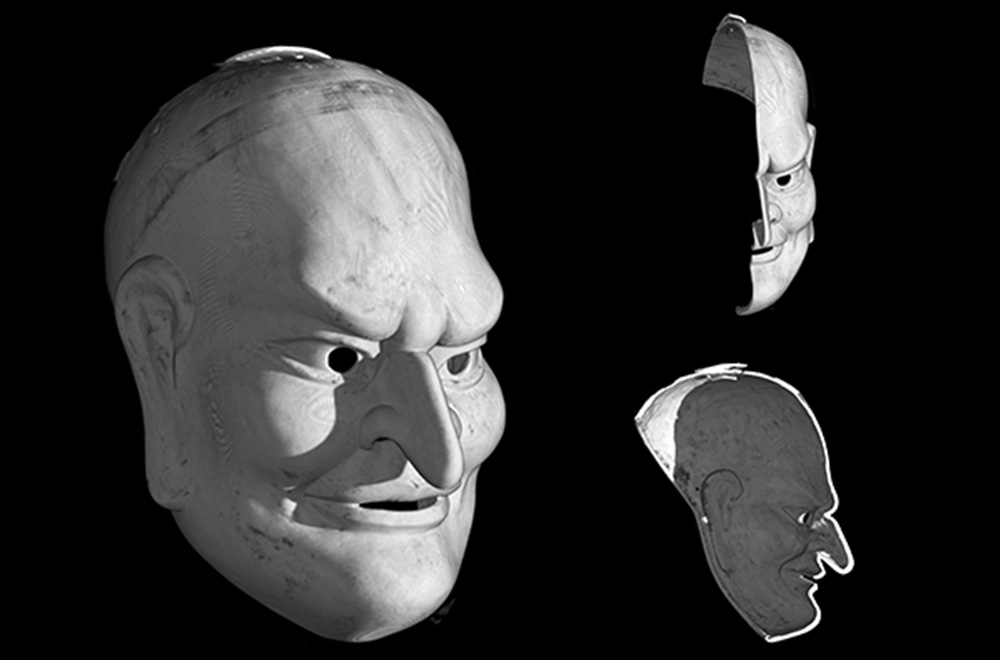
Hideyuki Tomisawa knows that a picture is worth at least a thousand words. He picks up a nautilus shell, almost as large as his hand, a curve of creamy white and light brown lines, and places it inside a scanning system He closes the door, and reaches out and pushes a switch. Seconds later, a PC monitor lights up and displays an image of the nautilus and the structural lines of the shell. It’s clear and detailed; it could be a blueprint.
On first hearing, nondestructive inspection sounds vaguely threating, just the opposite of what it is: a powerful tool that allows non-invasive, harmless examination and inspection of… just about everything. Most of us are familiar with it in its medical application, the X-rays, CT scanner and ultrasound systems that support diagnostics. But it’s also the technology that examines the secret interiors of historical artefacts, quickly inspects our luggage at airports, and provides industry with an essential and powerful tool.
Technology that sees through everything
As senior manager of the Sales and Engineering Department, Inspection and Mechatronics Systems Division at Toshiba IT & Control Systems Corporation (ITC), Tomisawa is an expert in nondestructive inspection. Pointing to the image of the nautilus, he explains: “Our industrial systems combine X-rays’ ability to penetrate objects with our advanced imaging technologies. Basically, we can see inside and inspect any object. I mean literally anything, except people and other living things.”
First, take your nautilus and position it
Inspect it
And reveal its secrets
Tomisawa explains how it all works
That ability makes nondestructive inspection a powerful ally for manufacturers in industries as diverse as aerospace, automobiles and semiconductors—anywhere where materials are molded or formed.
“Look at cars,” says Tomisawa. “Any defect in the parts or the materials they are made of could put lives risk lives. So manufacturers inspect moldings, looking for air bubbles that cause weakness. Semiconductor makers check circuit wiring for breaks and welds for integrity.”
Inspecting a wheel rim
Imaging defects in an aluminum casting
Tomisawa leads the way to another room, and like a proud father shows off ITC’s latest system, the TX Lamino. “It gets the most detailed images ever,” he explains. “It has a nano focus x-ray generator that realizes a 0.25-micron focal spot, and a 4-megapixel camera. Typical systems produce a 1-micron focal spot and have a 1-megapixel camera, so we get four times the resolution they do.”
The TX Lamino
The new system is also more accurate. Its name comes from laminography, a CT technology that tilts inspected objects and records images from different angles. This reveals defects that could well be missed when inspected only from one angle, and it’s a distinct advantage for inspecting circuit boards and other electrical parts.
Take a circuit board
Put it into the TX Lamino
And inspect its integrity
There’s also Toshiba’s know-how in imaging technology. The high resolution images are subjected to advanced image processing that improves correction and centers images, and then displayed on a 4K monitor that delivers lifelike realism. And that’s not all.
“TX Lamino takes multiple sliced images of objects and combines them in a realistic 3D image,” Tomisawa says. “We can also view each individual slice on the monitor in 3D, which really boosts accuracy. Think of a semiconductor; with a 2D image, it would be really easy to miss a disconnection. We catch them all.” He then produces another surprise, a copy of the nautilus, true in every detail. “The 3D data can also be fed to a 3D printer, and produces an exact copy.”
The perfectly copied nautilus
Just how exact is exact? Tomisawa brings out a motor cycle bearing and a resin copy that looks like the ghost of the original. It’s perfect in every detail—even an inner ring rotates like the original, friction free.
The bearing brothers
The inner ring rotates smoothly
Mapping the chambers of the nautilus
This video was released on February 21, 2016.
A safety technology with possibilities
After Tomisawa’s compelling demonstration, we are joined by Takashi Hashimoto, the former president and CEO of ITC and now an advisor to the company, who is more than happy to talk about ITC, its people and the future.
Hashimoto tells story of technological challenges
“Non-destructive inspection is very much a niche market in a way, but I am happy to see lots of young engineers who want to be involved in development work,” he says. “We need to see inside in more detail, and we are constantly working to refine our technology. As we work in industry, not people, we can explore different X-ray sources, and all sorts of possibilities. That’s what I see as the big difference from manufacturing simple measuring equipment. We see the hidden, and want to make it even more visible. That’s exciting for engineers.”
Non-destructive inspection system helps to evaluate parts, analyze causes of accidents and improve safety. But it is ready to do a lot more, according to Tomisawa.
“In the energy sector, it’s proving very successful in development of a new energy source, methane clathrate. We also have systems operation on battery production lines. Another possible application is medical manufacturing lines, and we are working with a pharmaceutical company on this. Medical production lines move rapidly, but as people take the final product, it is very important to avoid any contamination.”
The system incorporated into a battery production line
“A few generations ago, we relied on the ears of skilled craftsmen, who tapped objects and listened to the sound to assess quality,” says Hashimoto. “Today, we are doing all we can toremove uncertainty from inspections with highly accurate digital representations of the interior of objects. The great thing about this is that we are contributing to greater safety in everyday life for everybody.”