Spot Welding Inspection Robots Spark a Revolution in the Automotive Industry
2019/12/25 Toshiba Clip Team
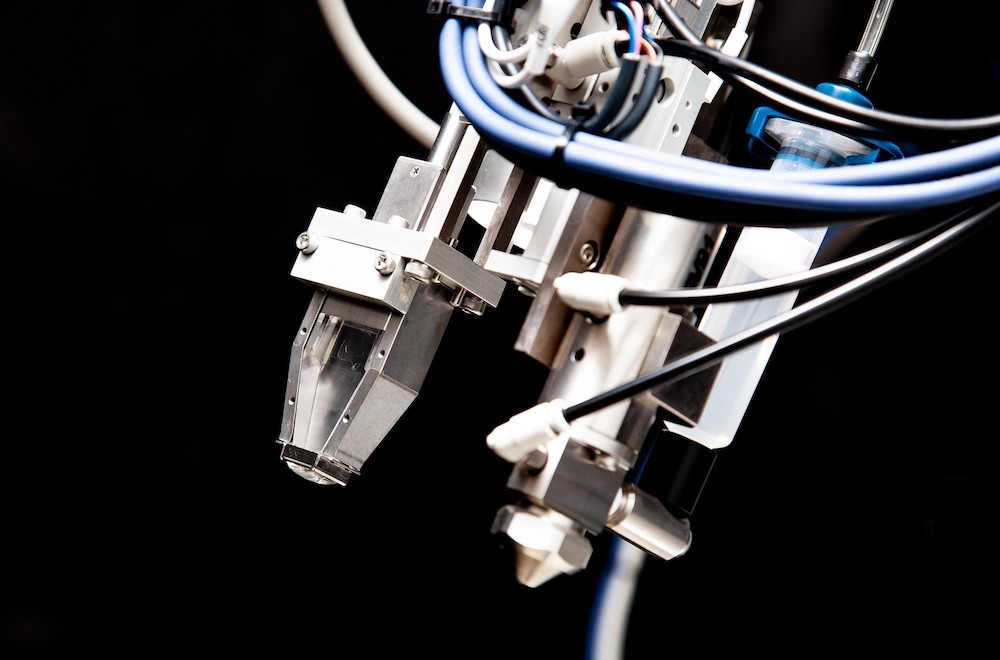
A single automobile consists of 30,000 or more individual parts. Every vehicle also has 4,000 – 5,000 places where the parts, such as metal plates, are spot welded together. Spot welding is a welding method that works by passing an electric current through metal plates and using heat generated from the electric resistance to weld the metal. It can be used to weld a variety of metals and is a common feature in many manufacturing processes because it offers several advantages, such as high welding speed, lower processing costs and the ability to reduce labour costs through the use of robots.
To ensure high quality, pulling sample parts off the production line and checking the strength of the spot welded places is an indispensable part of the manufacturing process. The standard method of quality inspection is to drive a chisel (a type of tool used to process metal) into the welded spot. If the joint does not break apart, it passes the test. However, if the weld is not strong enough, the piece is destroyed. Thus in addition to taking time and manual labour, this testing method is also very costly.
That is why Toshiba developed technology that allows welds to be inspected non-destructively and that, perhaps more importantly, allows the inspection to be performed automatically by robots. Approximately 95.6 million vehicles were produced globally in the year 2018, thus this technology represents the coming of a massive revolution to an equally massive industry.
Why smart, automated and non-destructive inspection is a better way to check welded parts
“Originally we would insert a chisel into the joint between metal plates and hit it with a hammer. Once we had confirmed the strength of the weld, we would return the deformed piece to normal. However, as cars become lighter and stronger in recent years, they are increasingly using high-strength steel sheets known as ‘high-tension materials.’ The properties of high-tension materials make it hard to insert chisels into them and also make it hard to return them to normal once they are deformed. Thus we are forced to destroy the welded spot in the course of the inspection.”
This is why the need for non-destructive inspection, which can verify welded parts without causing damage, is on the rise, explains Hiromasa Takahashi of the Mechatronics Engineering Solution Department, Corporate Manufacturing Engineering Center, Toshiba Corporation. Toshiba used the technology for medical use and power generation plants to develop an ultrasonic testing device known as Matrixeye™, and has been making progressive achievements in non-destructive inspection since 2004.
Hiromasa Takahashi, Mechatronics Engineering Solution Department, Corporate Manufacturing Engineering Center, Toshiba Corporation
Matrixeye™ is the world’s first 3D SAFT(Synthetic Aperture Focusing technique) inspection equipment with phased array function which enable higher resolution and high sensitivity.
“We use the reflection data of the ultrasound to visualize the strength of the weld points through 3D imaging. At the first stage, the processes of locating the weld, applying the couplant (contact catalyst) and operating the inspection probe must all be done by human beings. To obtain an accurate measurement, the inspection probe that emits the ultrasound is required to be applied to the welded part at an ideal angle. At the initial stage of the invention, knowing how to do that required a considerable degree of skill. All of this made inspections extremely time- and labour-intensive.” (Takahashi)
Matrixeye™ and the inspection probe that emits the ultrasound.
That was why the next challenge to be tackled in non-destructive inspection technology was creating structures for automating spot welding inspections through robot control.
Spot welding inspection robot (ultrasound inspection probe)
Work flow
How spot welding inspection robots work
Faster speeds with the tilt estimation engine
In order to inspect spot welds automatically, the inspection probe is required to maintain an appropriate level of parallelism while the Matrixeye™ is creating a 3D visualization of the joined part with ultrasound. This was normally achieved through manual techniques, so finding a way to maintain that parallelism automatically was a hurdle.
“For example, the first thing we tried was a method where we would find the place with the maximum nugget diameter (diameter of the junction) and then carry out sequential deformation of the parameters (tilt) from there to measure the maximum value. However that had a drawback because it needed several repeated measurements, which took at least 30 seconds.” (Takahashi)
After going through trial and error with a number of methods, they finally arrived at a solution: the tilt estimation engine.
“The tilt estimation engine is a new technology that automatically adjusts the measurement angle of the inspection probe. Based on the ultrasound reflection data measured by the Matrixeye™, it estimates the tilt of the welded part and then a robot automatically corrects the angle of the inspection probe. Through this, we are able to shrink inspection time from 30-40 seconds for human beings to approximately 7 seconds.” (Masahiro Saito, Mechatronics Engineering Solution Department, Corporate Manufacturing Engineering Center, Toshiba Corporation)
Automatic tilt adjustment
The consensus of the development team is that mere automation is meaningless unless it also produces higher speeds than manual processes can manage. Now that the technology is established after verification tests with a wide varieties of materials, he is confident that the efficiency gains delivered by the technology will bring great benefits to the automobile industry. Saito says the next challenge is obtaining further sample materials for testing.
This video was released on September 4, 2019.
“Right now, we are at the stage where we are working to improve usability while gathering as much testing data as possible by obtaining sample materials from various manufacturers and running verification tests on them. Going forward, we plan to listen more closely to the opinions and requests of those in the factories and use that to improve the user interface.” (Saito)
Masahiro Saito, Mechatronics Engineering Solution Department, Corporate Manufacturing Engineering Center, Toshiba Corporation
Great potential to apply technology to other industries and overseas
Toshiba is carrying out verification tests with the aim of launching this spot welding inspection technology within a year.
“For us, the first priority is planting the concept of automatic inspections in the field of automobile manufacturing. After that we will aim to make the technology capable of supporting more welding methods. It would be ideal if it could be adopted in airplane and ship manufacturing in the future. Naturally, we’re also hoping to deploy this technology overseas in future. Foreign manufacturers were highly enthusiastic about non-destructive inspection from the start, so I believe there is a huge market there.” (Takahashi)
This development of the technology has been aided by the integrated nature of the Research and Development Division at Toshiba, and the broad range of Toshiba’s internal technology assets.
“The Research & Development Division we belong to provides a fertile ground for using various in-house technologies together in a flexible way, so we were able to make effective use of Toshiba’s unique technologies. As the concept of MaaS (*) develops in the future, the number of public vehicles will most likely increase as well. To support this coming era, factories will be expected to put structures in place to enable them to provide high-quality vehicles in a speedy fashion. I believe our technology will contribute significantly to that process.” (Saito)
(*)Mobility as a Service: A new mobility concept where movement by all means of transportation, apart from privately-owned cars, is regarded as a single service and is linked seamlessly through the use of telecommunications regardless of the management body.
We look forward with great interest to seeing the transformations in manufacturing in the automotive industry in the coming years.
From left to right: Akira Ushijima, Masahiro Saito, Yasunori Chiba and Hiromasa Takahashi, members of the spot welding inspection robot development team of the Mechatronics Engineering Solution Department, Corporate Manufacturing Engineering Center, Toshiba Corporation.
Toshiba Spot Welding Inspection Robot:
http://cmc.toshiba.co.jp/cmc/en/rd/core/files/product/10e.pdf
Related Links
*This section contains links to websites operated by companies and organizations other than Toshiba Corporation.
Toshiba Inspection Solutions Co., Ltd.>3D ultrasonic inspection system (Matrixeye™) > Matrixeye™ ST for spot welding inspection